The Production Process of Mainstream Capacitors
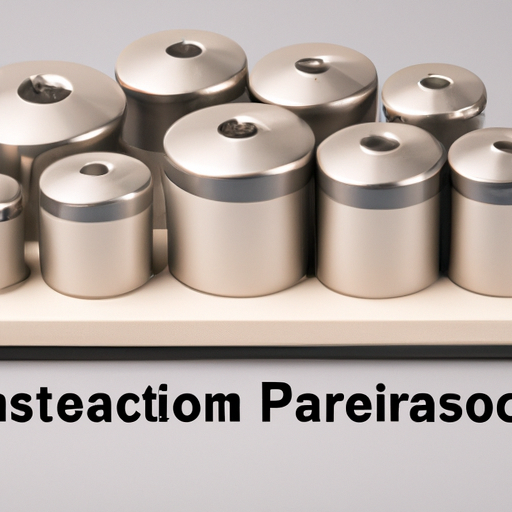
I. Introduction
Capacitors are essential components in modern electronic devices, serving as energy storage units that help regulate voltage and power flow. They play a critical role in various applications, from smoothing out electrical signals in power supplies to enabling rapid charge and discharge cycles in timing circuits. Understanding the production process of capacitors is vital for appreciating their significance in electronics. This blog post will explore the various types of capacitors, the raw materials used in their production, the manufacturing process, and the environmental considerations associated with their production.
II. Types of Capacitors
Capacitors come in various types, each designed for specific applications and performance characteristics.
A. Electrolytic Capacitors
Electrolytic capacitors are polarized components that offer high capacitance values in a relatively small size. They are commonly used in power supply circuits and audio applications.
B. Ceramic Capacitors
Ceramic capacitors are non-polarized and are known for their stability and reliability. They are widely used in high-frequency applications and are available in various capacitance values.
C. Film Capacitors
Film capacitors use a thin plastic film as the dielectric material. They are known for their low loss and high stability, making them suitable for audio and RF applications.
D. Tantalum Capacitors
Tantalum capacitors are known for their high capacitance and voltage ratings in a compact size. They are often used in military and aerospace applications due to their reliability.
E. Other Types
Other types of capacitors include supercapacitors, which offer high energy storage capabilities, and aluminum capacitors, which are commonly used in power electronics.
III. Raw Materials
The production of capacitors begins with the selection of raw materials, which significantly influence the performance and reliability of the final product.
A. Overview of Materials Used in Capacitor Production
1. **Dielectric Materials**: The dielectric material is crucial for a capacitor's function, as it separates the conductive plates and stores electrical energy. Common dielectric materials include ceramic, polyester, polypropylene, and tantalum oxide.
2. **Conductive Materials**: The electrodes of capacitors are typically made from conductive materials such as aluminum, tantalum, or conductive polymers.
3. **Electrolytes**: In electrolytic capacitors, electrolytes are used to enhance conductivity. These can be liquid or solid, depending on the capacitor type.
B. Sourcing and Quality Control of Raw Materials
Sourcing high-quality raw materials is essential for ensuring the performance and longevity of capacitors. Manufacturers often establish relationships with trusted suppliers and implement rigorous quality control measures to verify the purity and consistency of materials.
IV. Design and Engineering
The design and engineering phase is critical in determining the specifications and performance of the capacitor.
A. Initial Design Considerations
1. **Capacitance Value**: The desired capacitance value is determined based on the application requirements.
2. **Voltage Rating**: The voltage rating must be established to ensure the capacitor can handle the expected electrical stress.
3. **Size and Form Factor**: The physical dimensions of the capacitor are designed to fit within the constraints of the intended application.
B. Simulation and Modeling
Advanced simulation tools are used to model the electrical behavior of the capacitor under various conditions, allowing engineers to optimize the design before moving to prototyping.
C. Prototyping and Testing
Prototypes are created to validate the design. These prototypes undergo rigorous testing to ensure they meet the specified performance criteria.
V. Manufacturing Process
The manufacturing process of capacitors involves several key steps, each critical to producing a reliable product.
A. Step 1: Preparation of Dielectric Material
The first step involves preparing the dielectric material. Depending on the type of capacitor, this may include processes such as sintering for ceramic capacitors or film extrusion for film capacitors.
B. Step 2: Electrode Fabrication
Electrode fabrication involves selecting the appropriate conductive material and employing methods such as vapor deposition or etching to create the electrodes.
C. Step 3: Assembly of Capacitor
The assembly process involves layering the dielectric material and electrodes. Techniques such as winding or stacking are used to create the capacitor structure, ensuring proper alignment and spacing.
D. Step 4: Encapsulation
Encapsulation protects the capacitor from environmental factors and mechanical stress. Materials used for encapsulation can include epoxy resins or plastic housings, depending on the capacitor type.
E. Step 5: Electrical Connections
The final step involves making electrical connections, typically through soldering or terminal attachment. Quality assurance measures are implemented to ensure reliable connections.
VI. Testing and Quality Control
Testing is a crucial aspect of capacitor production, ensuring that each component meets the required specifications.
A. Importance of Testing in Capacitor Production
Testing helps identify defects and ensures that capacitors perform reliably in their intended applications.
B. Types of Tests Conducted
1. **Electrical Testing**: This includes measuring capacitance, leakage current, and equivalent series resistance (ESR).
2. **Environmental Testing**: Capacitors are subjected to temperature and humidity tests to assess their performance under various conditions.
3. **Reliability Testing**: Long-term reliability tests, such as life testing and accelerated aging, are conducted to predict the lifespan of the capacitor.
C. Quality Control Measures
Manufacturers implement strict quality control measures throughout the production process, including regular inspections and adherence to industry standards.
VII. Packaging and Distribution
Once capacitors pass testing, they are packaged and prepared for distribution.
A. Packaging Considerations
Packaging must protect the capacitors from physical damage and environmental factors during transport. Manufacturers often use anti-static materials and moisture barriers.
B. Distribution Channels
Capacitors are distributed through various channels, including direct sales to manufacturers, electronic component distributors, and online platforms.
C. Market Demand and Supply Chain Logistics
The demand for capacitors is influenced by trends in electronics, such as the growth of consumer electronics and renewable energy technologies. Efficient supply chain logistics are essential to meet market demands.
VIII. Environmental Considerations
The production of capacitors has environmental implications that manufacturers must address.
A. Impact of Capacitor Production on the Environment
The extraction of raw materials and the manufacturing process can contribute to environmental degradation. Manufacturers are increasingly aware of their ecological footprint.
B. Recycling and Disposal of Capacitors
Proper recycling and disposal methods are essential to minimize environmental impact. Many manufacturers are exploring ways to reclaim materials from used capacitors.
C. Sustainable Practices in Capacitor Manufacturing
Sustainable practices, such as using eco-friendly materials and reducing waste, are becoming more prevalent in the capacitor manufacturing industry.
IX. Conclusion
The production process of mainstream capacitors is a complex and multifaceted endeavor that involves careful consideration of materials, design, manufacturing techniques, and quality control. As technology advances, the demand for capacitors will continue to grow, driving innovation in capacitor design and production. Understanding this process not only highlights the importance of capacitors in electronic devices but also emphasizes the need for sustainable practices in their manufacturing. As we look to the future, capacitors will play a pivotal role in advancing electronic technology, enabling more efficient and powerful devices.
X. References
A comprehensive list of academic journals, industry reports, and manufacturer guidelines would typically follow to provide further reading and validation of the information presented in this blog post.
The Production Process of Mainstream Capacitors
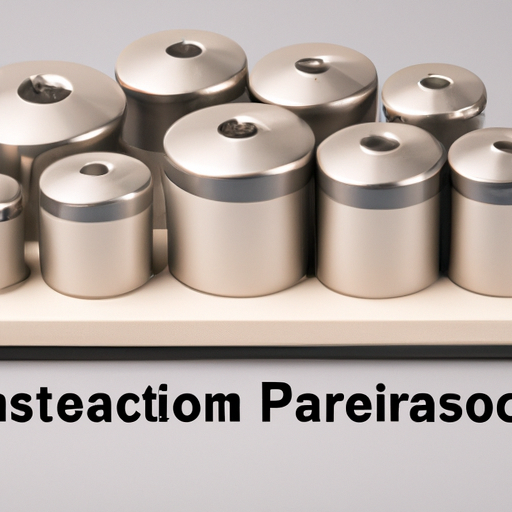
I. Introduction
Capacitors are essential components in modern electronic devices, serving as energy storage units that help regulate voltage and power flow. They play a critical role in various applications, from smoothing out electrical signals in power supplies to enabling rapid charge and discharge cycles in timing circuits. Understanding the production process of capacitors is vital for appreciating their significance in electronics. This blog post will explore the various types of capacitors, the raw materials used in their production, the manufacturing process, and the environmental considerations associated with their production.
II. Types of Capacitors
Capacitors come in various types, each designed for specific applications and performance characteristics.
A. Electrolytic Capacitors
Electrolytic capacitors are polarized components that offer high capacitance values in a relatively small size. They are commonly used in power supply circuits and audio applications.
B. Ceramic Capacitors
Ceramic capacitors are non-polarized and are known for their stability and reliability. They are widely used in high-frequency applications and are available in various capacitance values.
C. Film Capacitors
Film capacitors use a thin plastic film as the dielectric material. They are known for their low loss and high stability, making them suitable for audio and RF applications.
D. Tantalum Capacitors
Tantalum capacitors are known for their high capacitance and voltage ratings in a compact size. They are often used in military and aerospace applications due to their reliability.
E. Other Types
Other types of capacitors include supercapacitors, which offer high energy storage capabilities, and aluminum capacitors, which are commonly used in power electronics.
III. Raw Materials
The production of capacitors begins with the selection of raw materials, which significantly influence the performance and reliability of the final product.
A. Overview of Materials Used in Capacitor Production
1. **Dielectric Materials**: The dielectric material is crucial for a capacitor's function, as it separates the conductive plates and stores electrical energy. Common dielectric materials include ceramic, polyester, polypropylene, and tantalum oxide.
2. **Conductive Materials**: The electrodes of capacitors are typically made from conductive materials such as aluminum, tantalum, or conductive polymers.
3. **Electrolytes**: In electrolytic capacitors, electrolytes are used to enhance conductivity. These can be liquid or solid, depending on the capacitor type.
B. Sourcing and Quality Control of Raw Materials
Sourcing high-quality raw materials is essential for ensuring the performance and longevity of capacitors. Manufacturers often establish relationships with trusted suppliers and implement rigorous quality control measures to verify the purity and consistency of materials.
IV. Design and Engineering
The design and engineering phase is critical in determining the specifications and performance of the capacitor.
A. Initial Design Considerations
1. **Capacitance Value**: The desired capacitance value is determined based on the application requirements.
2. **Voltage Rating**: The voltage rating must be established to ensure the capacitor can handle the expected electrical stress.
3. **Size and Form Factor**: The physical dimensions of the capacitor are designed to fit within the constraints of the intended application.
B. Simulation and Modeling
Advanced simulation tools are used to model the electrical behavior of the capacitor under various conditions, allowing engineers to optimize the design before moving to prototyping.
C. Prototyping and Testing
Prototypes are created to validate the design. These prototypes undergo rigorous testing to ensure they meet the specified performance criteria.
V. Manufacturing Process
The manufacturing process of capacitors involves several key steps, each critical to producing a reliable product.
A. Step 1: Preparation of Dielectric Material
The first step involves preparing the dielectric material. Depending on the type of capacitor, this may include processes such as sintering for ceramic capacitors or film extrusion for film capacitors.
B. Step 2: Electrode Fabrication
Electrode fabrication involves selecting the appropriate conductive material and employing methods such as vapor deposition or etching to create the electrodes.
C. Step 3: Assembly of Capacitor
The assembly process involves layering the dielectric material and electrodes. Techniques such as winding or stacking are used to create the capacitor structure, ensuring proper alignment and spacing.
D. Step 4: Encapsulation
Encapsulation protects the capacitor from environmental factors and mechanical stress. Materials used for encapsulation can include epoxy resins or plastic housings, depending on the capacitor type.
E. Step 5: Electrical Connections
The final step involves making electrical connections, typically through soldering or terminal attachment. Quality assurance measures are implemented to ensure reliable connections.
VI. Testing and Quality Control
Testing is a crucial aspect of capacitor production, ensuring that each component meets the required specifications.
A. Importance of Testing in Capacitor Production
Testing helps identify defects and ensures that capacitors perform reliably in their intended applications.
B. Types of Tests Conducted
1. **Electrical Testing**: This includes measuring capacitance, leakage current, and equivalent series resistance (ESR).
2. **Environmental Testing**: Capacitors are subjected to temperature and humidity tests to assess their performance under various conditions.
3. **Reliability Testing**: Long-term reliability tests, such as life testing and accelerated aging, are conducted to predict the lifespan of the capacitor.
C. Quality Control Measures
Manufacturers implement strict quality control measures throughout the production process, including regular inspections and adherence to industry standards.
VII. Packaging and Distribution
Once capacitors pass testing, they are packaged and prepared for distribution.
A. Packaging Considerations
Packaging must protect the capacitors from physical damage and environmental factors during transport. Manufacturers often use anti-static materials and moisture barriers.
B. Distribution Channels
Capacitors are distributed through various channels, including direct sales to manufacturers, electronic component distributors, and online platforms.
C. Market Demand and Supply Chain Logistics
The demand for capacitors is influenced by trends in electronics, such as the growth of consumer electronics and renewable energy technologies. Efficient supply chain logistics are essential to meet market demands.
VIII. Environmental Considerations
The production of capacitors has environmental implications that manufacturers must address.
A. Impact of Capacitor Production on the Environment
The extraction of raw materials and the manufacturing process can contribute to environmental degradation. Manufacturers are increasingly aware of their ecological footprint.
B. Recycling and Disposal of Capacitors
Proper recycling and disposal methods are essential to minimize environmental impact. Many manufacturers are exploring ways to reclaim materials from used capacitors.
C. Sustainable Practices in Capacitor Manufacturing
Sustainable practices, such as using eco-friendly materials and reducing waste, are becoming more prevalent in the capacitor manufacturing industry.
IX. Conclusion
The production process of mainstream capacitors is a complex and multifaceted endeavor that involves careful consideration of materials, design, manufacturing techniques, and quality control. As technology advances, the demand for capacitors will continue to grow, driving innovation in capacitor design and production. Understanding this process not only highlights the importance of capacitors in electronic devices but also emphasizes the need for sustainable practices in their manufacturing. As we look to the future, capacitors will play a pivotal role in advancing electronic technology, enabling more efficient and powerful devices.
X. References
A comprehensive list of academic journals, industry reports, and manufacturer guidelines would typically follow to provide further reading and validation of the information presented in this blog post.