Manufacturing Processes of the Latest Current Sensing Resistors
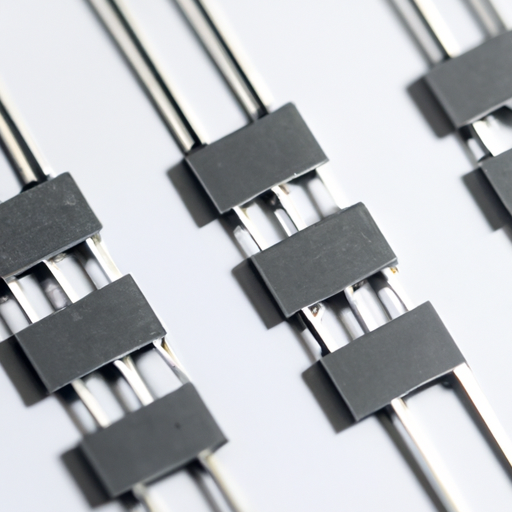
I. Introduction
Current sensing resistors are essential components in modern electronics, playing a critical role in monitoring and controlling electrical currents in various applications. These resistors allow for precise measurement of current flow, enabling systems to operate efficiently and safely. As technology advances, the demand for more accurate, reliable, and compact current sensing solutions has led to significant innovations in their manufacturing processes. This blog post will explore the various types of current sensing resistors, the raw materials used in their production, the detailed manufacturing processes, and the future trends shaping this industry.
II. Types of Current Sensing Resistors
Current sensing resistors come in several types, each with unique characteristics suited for specific applications:
A. Shunt Resistors
Shunt resistors are low-resistance components placed in series with a load to measure the current flowing through it. They are widely used in power management systems and battery monitoring applications.
B. Wire-Wound Resistors
These resistors are made by winding a wire around a core, providing high precision and stability. They are often used in high-power applications due to their ability to handle significant current loads.
C. Thin-Film Resistors
Thin-film resistors are created by depositing a thin layer of resistive material onto a substrate. They offer excellent accuracy and temperature stability, making them ideal for precision applications.
D. Thick-Film Resistors
Thick-film resistors are produced by printing a thick layer of resistive paste onto a substrate. They are cost-effective and suitable for mass production, commonly used in consumer electronics.
E. Comparison of Different Types
Each type of current sensing resistor has its advantages and disadvantages, making them suitable for different applications. Shunt resistors are favored for their simplicity, while thin-film resistors excel in precision. Understanding these differences is crucial for selecting the right resistor for a specific application.
III. Raw Materials Used in Manufacturing
The performance of current sensing resistors heavily depends on the quality of the raw materials used in their production.
A. Conductive Materials
1. **Copper**: Known for its excellent conductivity, copper is often used in shunt and wire-wound resistors.
2. **Nickel**: Nickel is used for its corrosion resistance and stability, particularly in thin-film applications.
3. **Manganese**: Manganese is sometimes used in combination with other materials to enhance the resistive properties of certain resistors.
B. Substrate Materials
1. **Ceramic**: Ceramic substrates provide excellent thermal stability and are commonly used in thick-film resistors.
2. **Epoxy**: Epoxy materials are used for their insulating properties and are often found in encapsulated resistors.
3. **Metal**: Metal substrates are used in high-power applications due to their ability to dissipate heat effectively.
C. Insulating Materials
1. **Glass**: Glass is used for its high dielectric strength and thermal stability, making it suitable for high-performance applications.
2. **Polyimide**: This flexible insulating material is often used in applications requiring high-temperature resistance.
IV. Manufacturing Processes
The manufacturing of current sensing resistors involves several key processes, each critical to ensuring the final product meets performance standards.
A. Design and Prototyping
1. **Computer-aided design (CAD)**: Modern manufacturing begins with CAD software, allowing engineers to create precise designs and layouts for resistors.
2. **Simulation and testing**: Before production, simulations are conducted to predict performance and identify potential issues.
B. Material Preparation
1. **Sourcing and quality control**: High-quality raw materials are sourced from reliable suppliers, with rigorous quality control measures in place to ensure consistency.
2. **Material processing techniques**: Materials undergo various processing techniques, such as alloying and purification, to achieve the desired properties.
C. Fabrication Techniques
1. **Thin-film deposition**:
- **Sputtering**: This technique involves bombarding a target material with ions to deposit a thin film onto a substrate.
- **Chemical vapor deposition (CVD)**: CVD uses chemical reactions to produce thin films, offering excellent uniformity and control over thickness.
2. **Thick-film printing**:
- **Screen printing**: A resistive paste is printed onto a substrate using a mesh screen, allowing for precise patterns.
- **Inkjet printing**: This method uses inkjet technology to deposit resistive materials, enabling complex designs and rapid prototyping.
3. **Wire-wound techniques**:
- **Winding processes**: Wire is wound around a core to create the desired resistance value, with careful attention to the number of turns and wire gauge.
- **Resistance adjustment**: After winding, the resistance is fine-tuned through trimming or additional processing.
D. Assembly and Packaging
1. **Mounting on substrates**: Resistors are mounted onto various substrates, ensuring proper alignment and connectivity.
2. **Encapsulation and protection**: Encapsulation materials protect resistors from environmental factors, enhancing durability and reliability.
E. Testing and Quality Assurance
1. **Electrical testing**: Each resistor undergoes electrical testing to verify its resistance value and performance characteristics.
2. **Environmental testing**: Resistors are subjected to various environmental conditions to ensure they can withstand temperature fluctuations, humidity, and other factors.
3. **Reliability testing**: Long-term reliability tests are conducted to assess the lifespan and performance stability of the resistors.
V. Innovations in Current Sensing Resistor Manufacturing
The manufacturing processes for current sensing resistors are continually evolving, driven by advancements in technology and materials science.
A. Advances in Materials Science
New materials are being developed to enhance the performance of current sensing resistors, including composites and nanomaterials that offer improved conductivity and stability.
B. Automation and Industry 4.0
The integration of automation and smart manufacturing technologies is streamlining production processes, reducing costs, and improving quality control.
C. Miniaturization and Integration with Other Components
As electronic devices become smaller and more complex, there is a growing trend toward miniaturizing current sensing resistors and integrating them with other components, such as microcontrollers and sensors.
D. Sustainability and Eco-friendly Practices
Manufacturers are increasingly focusing on sustainable practices, including the use of eco-friendly materials and processes that minimize waste and energy consumption.
VI. Challenges in Manufacturing Current Sensing Resistors
Despite advancements, the manufacturing of current sensing resistors faces several challenges:
A. Precision and Accuracy Requirements
The need for high precision and accuracy in current sensing applications places significant demands on manufacturing processes, requiring continuous improvements and innovations.
B. Cost Management
Balancing quality with cost-effectiveness is a constant challenge, particularly as raw material prices fluctuate and competition increases.
C. Supply Chain Issues
Global supply chain disruptions can impact the availability of critical materials, affecting production timelines and costs.
D. Meeting Regulatory Standards
Manufacturers must navigate complex regulatory environments to ensure their products meet safety and performance standards.
VII. Future Trends in Current Sensing Resistor Manufacturing
The future of current sensing resistor manufacturing is poised for exciting developments:
A. Emerging Technologies
New technologies, such as 3D printing and advanced nanofabrication techniques, are expected to revolutionize the production of current sensing resistors.
B. Market Demand and Applications
As the demand for electric vehicles, renewable energy systems, and smart devices continues to grow, the need for advanced current sensing solutions will increase.
C. Potential for New Materials and Designs
Research into new materials, such as graphene and other nanomaterials, holds promise for creating resistors with superior performance characteristics.
VIII. Conclusion
Current sensing resistors are vital components in modern electronics, enabling precise current measurement and control. The manufacturing processes for these resistors are complex and continually evolving, driven by advancements in materials science, automation, and market demands. As the industry faces challenges related to precision, cost, and regulatory compliance, the future holds exciting possibilities for innovation and growth. By understanding the manufacturing processes and trends, stakeholders can better navigate the landscape of current sensing resistors and contribute to the development of more efficient and reliable electronic systems.
Manufacturing Processes of the Latest Current Sensing Resistors
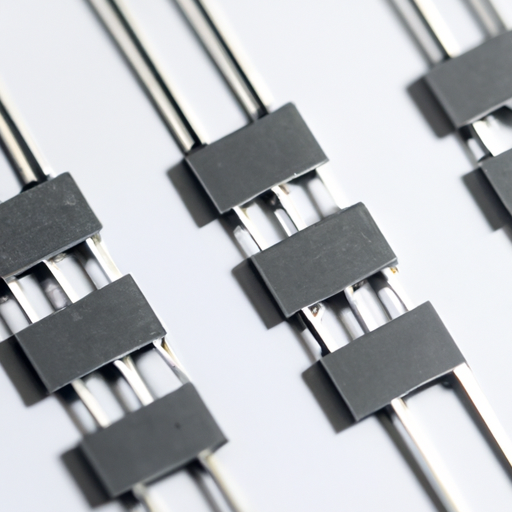
I. Introduction
Current sensing resistors are essential components in modern electronics, playing a critical role in monitoring and controlling electrical currents in various applications. These resistors allow for precise measurement of current flow, enabling systems to operate efficiently and safely. As technology advances, the demand for more accurate, reliable, and compact current sensing solutions has led to significant innovations in their manufacturing processes. This blog post will explore the various types of current sensing resistors, the raw materials used in their production, the detailed manufacturing processes, and the future trends shaping this industry.
II. Types of Current Sensing Resistors
Current sensing resistors come in several types, each with unique characteristics suited for specific applications:
A. Shunt Resistors
Shunt resistors are low-resistance components placed in series with a load to measure the current flowing through it. They are widely used in power management systems and battery monitoring applications.
B. Wire-Wound Resistors
These resistors are made by winding a wire around a core, providing high precision and stability. They are often used in high-power applications due to their ability to handle significant current loads.
C. Thin-Film Resistors
Thin-film resistors are created by depositing a thin layer of resistive material onto a substrate. They offer excellent accuracy and temperature stability, making them ideal for precision applications.
D. Thick-Film Resistors
Thick-film resistors are produced by printing a thick layer of resistive paste onto a substrate. They are cost-effective and suitable for mass production, commonly used in consumer electronics.
E. Comparison of Different Types
Each type of current sensing resistor has its advantages and disadvantages, making them suitable for different applications. Shunt resistors are favored for their simplicity, while thin-film resistors excel in precision. Understanding these differences is crucial for selecting the right resistor for a specific application.
III. Raw Materials Used in Manufacturing
The performance of current sensing resistors heavily depends on the quality of the raw materials used in their production.
A. Conductive Materials
1. **Copper**: Known for its excellent conductivity, copper is often used in shunt and wire-wound resistors.
2. **Nickel**: Nickel is used for its corrosion resistance and stability, particularly in thin-film applications.
3. **Manganese**: Manganese is sometimes used in combination with other materials to enhance the resistive properties of certain resistors.
B. Substrate Materials
1. **Ceramic**: Ceramic substrates provide excellent thermal stability and are commonly used in thick-film resistors.
2. **Epoxy**: Epoxy materials are used for their insulating properties and are often found in encapsulated resistors.
3. **Metal**: Metal substrates are used in high-power applications due to their ability to dissipate heat effectively.
C. Insulating Materials
1. **Glass**: Glass is used for its high dielectric strength and thermal stability, making it suitable for high-performance applications.
2. **Polyimide**: This flexible insulating material is often used in applications requiring high-temperature resistance.
IV. Manufacturing Processes
The manufacturing of current sensing resistors involves several key processes, each critical to ensuring the final product meets performance standards.
A. Design and Prototyping
1. **Computer-aided design (CAD)**: Modern manufacturing begins with CAD software, allowing engineers to create precise designs and layouts for resistors.
2. **Simulation and testing**: Before production, simulations are conducted to predict performance and identify potential issues.
B. Material Preparation
1. **Sourcing and quality control**: High-quality raw materials are sourced from reliable suppliers, with rigorous quality control measures in place to ensure consistency.
2. **Material processing techniques**: Materials undergo various processing techniques, such as alloying and purification, to achieve the desired properties.
C. Fabrication Techniques
1. **Thin-film deposition**:
- **Sputtering**: This technique involves bombarding a target material with ions to deposit a thin film onto a substrate.
- **Chemical vapor deposition (CVD)**: CVD uses chemical reactions to produce thin films, offering excellent uniformity and control over thickness.
2. **Thick-film printing**:
- **Screen printing**: A resistive paste is printed onto a substrate using a mesh screen, allowing for precise patterns.
- **Inkjet printing**: This method uses inkjet technology to deposit resistive materials, enabling complex designs and rapid prototyping.
3. **Wire-wound techniques**:
- **Winding processes**: Wire is wound around a core to create the desired resistance value, with careful attention to the number of turns and wire gauge.
- **Resistance adjustment**: After winding, the resistance is fine-tuned through trimming or additional processing.
D. Assembly and Packaging
1. **Mounting on substrates**: Resistors are mounted onto various substrates, ensuring proper alignment and connectivity.
2. **Encapsulation and protection**: Encapsulation materials protect resistors from environmental factors, enhancing durability and reliability.
E. Testing and Quality Assurance
1. **Electrical testing**: Each resistor undergoes electrical testing to verify its resistance value and performance characteristics.
2. **Environmental testing**: Resistors are subjected to various environmental conditions to ensure they can withstand temperature fluctuations, humidity, and other factors.
3. **Reliability testing**: Long-term reliability tests are conducted to assess the lifespan and performance stability of the resistors.
V. Innovations in Current Sensing Resistor Manufacturing
The manufacturing processes for current sensing resistors are continually evolving, driven by advancements in technology and materials science.
A. Advances in Materials Science
New materials are being developed to enhance the performance of current sensing resistors, including composites and nanomaterials that offer improved conductivity and stability.
B. Automation and Industry 4.0
The integration of automation and smart manufacturing technologies is streamlining production processes, reducing costs, and improving quality control.
C. Miniaturization and Integration with Other Components
As electronic devices become smaller and more complex, there is a growing trend toward miniaturizing current sensing resistors and integrating them with other components, such as microcontrollers and sensors.
D. Sustainability and Eco-friendly Practices
Manufacturers are increasingly focusing on sustainable practices, including the use of eco-friendly materials and processes that minimize waste and energy consumption.
VI. Challenges in Manufacturing Current Sensing Resistors
Despite advancements, the manufacturing of current sensing resistors faces several challenges:
A. Precision and Accuracy Requirements
The need for high precision and accuracy in current sensing applications places significant demands on manufacturing processes, requiring continuous improvements and innovations.
B. Cost Management
Balancing quality with cost-effectiveness is a constant challenge, particularly as raw material prices fluctuate and competition increases.
C. Supply Chain Issues
Global supply chain disruptions can impact the availability of critical materials, affecting production timelines and costs.
D. Meeting Regulatory Standards
Manufacturers must navigate complex regulatory environments to ensure their products meet safety and performance standards.
VII. Future Trends in Current Sensing Resistor Manufacturing
The future of current sensing resistor manufacturing is poised for exciting developments:
A. Emerging Technologies
New technologies, such as 3D printing and advanced nanofabrication techniques, are expected to revolutionize the production of current sensing resistors.
B. Market Demand and Applications
As the demand for electric vehicles, renewable energy systems, and smart devices continues to grow, the need for advanced current sensing solutions will increase.
C. Potential for New Materials and Designs
Research into new materials, such as graphene and other nanomaterials, holds promise for creating resistors with superior performance characteristics.
VIII. Conclusion
Current sensing resistors are vital components in modern electronics, enabling precise current measurement and control. The manufacturing processes for these resistors are complex and continually evolving, driven by advancements in materials science, automation, and market demands. As the industry faces challenges related to precision, cost, and regulatory compliance, the future holds exciting possibilities for innovation and growth. By understanding the manufacturing processes and trends, stakeholders can better navigate the landscape of current sensing resistors and contribute to the development of more efficient and reliable electronic systems.