Common Production Processes for Metal Resistors
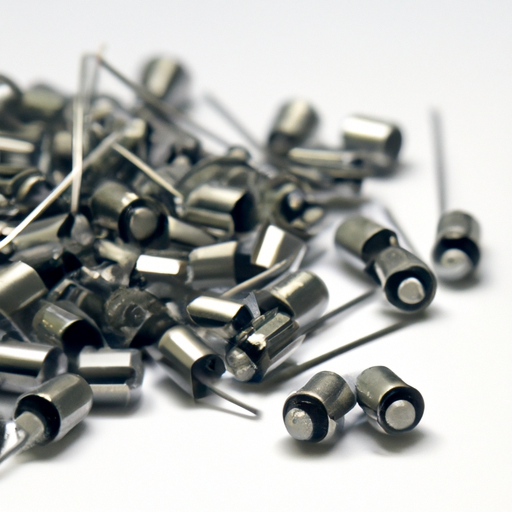
I. Introduction
In the realm of electronics, resistors play a pivotal role in controlling the flow of electric current. Among the various types of resistors, metal resistors are particularly valued for their stability, precision, and reliability. These components are essential in a wide array of applications, from consumer electronics to industrial machinery. Understanding the production processes behind metal resistors not only sheds light on their functionality but also highlights the intricate craftsmanship involved in their creation.
II. Types of Metal Resistors
A. Metal Film Resistors
Metal film resistors are known for their high precision and low noise characteristics. They are made by depositing a thin layer of metal onto a ceramic substrate, which allows for precise control over resistance values. These resistors are commonly used in applications requiring high accuracy, such as in measurement devices and audio equipment.
B. Metal Oxide Resistors
Metal oxide resistors are constructed using a metal oxide film, which provides excellent thermal stability and high resistance to environmental factors. They are often used in power applications due to their ability to handle high voltages and currents. Their robustness makes them suitable for automotive and industrial applications.
C. Wirewound Resistors
Wirewound resistors are made by winding a metal wire around a core, typically made of ceramic or fiberglass. This design allows for high power ratings and excellent heat dissipation. Wirewound resistors are frequently used in applications where high power and precision are required, such as in power supplies and audio amplifiers.
III. Raw Materials Used in Metal Resistor Production
A. Types of Metals Used
1. **Nickel**: Known for its corrosion resistance and stability, nickel is often used in metal film resistors.
2. **Copper**: Due to its excellent conductivity, copper is commonly used in wirewound resistors.
3. **Tin**: Tin is frequently used as a coating material to enhance the solderability of resistor leads.
B. Insulating Materials
1. **Ceramic Substrates**: These are used in metal film and wirewound resistors for their excellent thermal and electrical insulating properties.
2. **Epoxy Resins**: Epoxy is often used as a protective coating for resistors, providing durability and resistance to environmental factors.
IV. Common Production Processes
A. Design and Engineering
The production of metal resistors begins with design and engineering. This phase involves defining specifications and requirements based on the intended application. Engineers create prototypes to test various designs, ensuring that the final product meets performance standards.
B. Material Preparation
Once the design is finalized, the next step is material preparation. This involves sourcing high-quality raw materials and conducting rigorous quality control checks. The materials are then processed to meet the specific requirements for resistor production.
C. Fabrication Techniques
1. **Thin Film Deposition**: This technique is crucial for producing metal film resistors. It involves depositing a thin layer of metal onto a substrate using methods such as:
- **Sputtering**: A process where metal atoms are ejected from a target and deposited onto the substrate.
- **Evaporation**: In this method, metal is heated until it vaporizes and then condenses on the cooler substrate.
2. **Thick Film Printing**: Used primarily for metal oxide resistors, this technique involves screen printing a paste made of metal oxides onto a substrate. Key steps include:
- **Screen Printing**: A stencil is used to apply the paste in precise patterns.
- **Ink Formulation**: The composition of the paste is carefully controlled to achieve the desired resistance values.
3. **Wirewound Techniques**: For wirewound resistors, the fabrication process includes:
- **Wire Winding**: A metal wire is wound around a core to create the resistor.
- **Core Preparation**: The core material is selected based on the required thermal and electrical properties.
D. Assembly
After fabrication, the resistors undergo assembly. This involves mounting the resistors onto substrates and making electrical connections through soldering. Proper assembly is crucial for ensuring the reliability and performance of the final product.
E. Testing and Quality Control
Quality control is a critical aspect of resistor production. Various testing methods are employed to ensure that the resistors meet electrical and environmental standards. This includes:
1. **Electrical Testing**: Resistors are tested for resistance values, tolerance, and temperature coefficients.
2. **Environmental Testing**: Resistors are subjected to extreme conditions, such as temperature and humidity, to assess their durability.
3. **Reliability Assessments**: Long-term testing is conducted to evaluate the lifespan and performance stability of the resistors.
V. Post-Production Processes
A. Packaging
Once the resistors pass quality control, they are packaged for distribution. The choice of packaging materials is essential for protecting the resistors from physical damage and environmental factors. Proper packaging also plays a role in maintaining the performance characteristics of the resistors during transport and storage.
B. Distribution
The distribution of metal resistors involves navigating a complex supply chain. Manufacturers must consider market demand and trends to ensure that they meet the needs of their customers. Efficient distribution channels are vital for delivering products to various markets, from consumer electronics to industrial applications.
VI. Innovations and Future Trends in Metal Resistor Production
A. Advances in Materials Science
Ongoing research in materials science is leading to the development of new materials that enhance the performance of metal resistors. Innovations such as nanomaterials and advanced composites are being explored to improve resistance stability and reduce size.
B. Automation and Industry 4.0
The integration of automation and Industry 4.0 technologies is transforming the production processes of metal resistors. Smart manufacturing techniques, including robotics and data analytics, are being implemented to increase efficiency and reduce production costs.
C. Environmental Considerations and Sustainability
As the electronics industry faces increasing pressure to adopt sustainable practices, metal resistor manufacturers are exploring eco-friendly materials and production methods. This includes reducing waste, recycling materials, and minimizing energy consumption during production.
VII. Conclusion
In summary, the production processes for metal resistors are complex and multifaceted, involving various types of resistors, raw materials, and fabrication techniques. Understanding these processes is crucial for appreciating the role of resistors in electronic circuits and the advancements being made in the field. As technology continues to evolve, the future of metal resistors looks promising, with innovations in materials science, automation, and sustainability paving the way for enhanced performance and reliability in electronic applications.
Common Production Processes for Metal Resistors
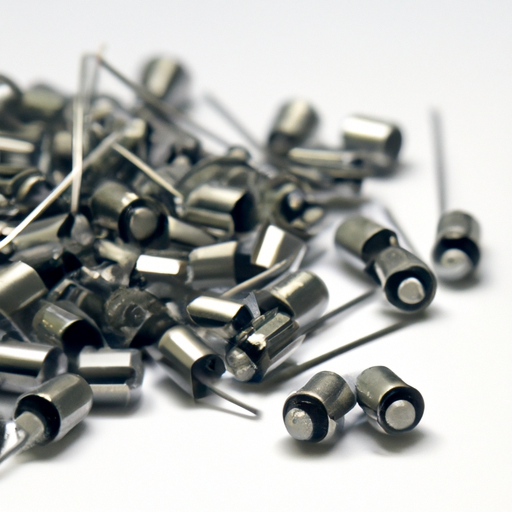
I. Introduction
In the realm of electronics, resistors play a pivotal role in controlling the flow of electric current. Among the various types of resistors, metal resistors are particularly valued for their stability, precision, and reliability. These components are essential in a wide array of applications, from consumer electronics to industrial machinery. Understanding the production processes behind metal resistors not only sheds light on their functionality but also highlights the intricate craftsmanship involved in their creation.
II. Types of Metal Resistors
A. Metal Film Resistors
Metal film resistors are known for their high precision and low noise characteristics. They are made by depositing a thin layer of metal onto a ceramic substrate, which allows for precise control over resistance values. These resistors are commonly used in applications requiring high accuracy, such as in measurement devices and audio equipment.
B. Metal Oxide Resistors
Metal oxide resistors are constructed using a metal oxide film, which provides excellent thermal stability and high resistance to environmental factors. They are often used in power applications due to their ability to handle high voltages and currents. Their robustness makes them suitable for automotive and industrial applications.
C. Wirewound Resistors
Wirewound resistors are made by winding a metal wire around a core, typically made of ceramic or fiberglass. This design allows for high power ratings and excellent heat dissipation. Wirewound resistors are frequently used in applications where high power and precision are required, such as in power supplies and audio amplifiers.
III. Raw Materials Used in Metal Resistor Production
A. Types of Metals Used
1. **Nickel**: Known for its corrosion resistance and stability, nickel is often used in metal film resistors.
2. **Copper**: Due to its excellent conductivity, copper is commonly used in wirewound resistors.
3. **Tin**: Tin is frequently used as a coating material to enhance the solderability of resistor leads.
B. Insulating Materials
1. **Ceramic Substrates**: These are used in metal film and wirewound resistors for their excellent thermal and electrical insulating properties.
2. **Epoxy Resins**: Epoxy is often used as a protective coating for resistors, providing durability and resistance to environmental factors.
IV. Common Production Processes
A. Design and Engineering
The production of metal resistors begins with design and engineering. This phase involves defining specifications and requirements based on the intended application. Engineers create prototypes to test various designs, ensuring that the final product meets performance standards.
B. Material Preparation
Once the design is finalized, the next step is material preparation. This involves sourcing high-quality raw materials and conducting rigorous quality control checks. The materials are then processed to meet the specific requirements for resistor production.
C. Fabrication Techniques
1. **Thin Film Deposition**: This technique is crucial for producing metal film resistors. It involves depositing a thin layer of metal onto a substrate using methods such as:
- **Sputtering**: A process where metal atoms are ejected from a target and deposited onto the substrate.
- **Evaporation**: In this method, metal is heated until it vaporizes and then condenses on the cooler substrate.
2. **Thick Film Printing**: Used primarily for metal oxide resistors, this technique involves screen printing a paste made of metal oxides onto a substrate. Key steps include:
- **Screen Printing**: A stencil is used to apply the paste in precise patterns.
- **Ink Formulation**: The composition of the paste is carefully controlled to achieve the desired resistance values.
3. **Wirewound Techniques**: For wirewound resistors, the fabrication process includes:
- **Wire Winding**: A metal wire is wound around a core to create the resistor.
- **Core Preparation**: The core material is selected based on the required thermal and electrical properties.
D. Assembly
After fabrication, the resistors undergo assembly. This involves mounting the resistors onto substrates and making electrical connections through soldering. Proper assembly is crucial for ensuring the reliability and performance of the final product.
E. Testing and Quality Control
Quality control is a critical aspect of resistor production. Various testing methods are employed to ensure that the resistors meet electrical and environmental standards. This includes:
1. **Electrical Testing**: Resistors are tested for resistance values, tolerance, and temperature coefficients.
2. **Environmental Testing**: Resistors are subjected to extreme conditions, such as temperature and humidity, to assess their durability.
3. **Reliability Assessments**: Long-term testing is conducted to evaluate the lifespan and performance stability of the resistors.
V. Post-Production Processes
A. Packaging
Once the resistors pass quality control, they are packaged for distribution. The choice of packaging materials is essential for protecting the resistors from physical damage and environmental factors. Proper packaging also plays a role in maintaining the performance characteristics of the resistors during transport and storage.
B. Distribution
The distribution of metal resistors involves navigating a complex supply chain. Manufacturers must consider market demand and trends to ensure that they meet the needs of their customers. Efficient distribution channels are vital for delivering products to various markets, from consumer electronics to industrial applications.
VI. Innovations and Future Trends in Metal Resistor Production
A. Advances in Materials Science
Ongoing research in materials science is leading to the development of new materials that enhance the performance of metal resistors. Innovations such as nanomaterials and advanced composites are being explored to improve resistance stability and reduce size.
B. Automation and Industry 4.0
The integration of automation and Industry 4.0 technologies is transforming the production processes of metal resistors. Smart manufacturing techniques, including robotics and data analytics, are being implemented to increase efficiency and reduce production costs.
C. Environmental Considerations and Sustainability
As the electronics industry faces increasing pressure to adopt sustainable practices, metal resistor manufacturers are exploring eco-friendly materials and production methods. This includes reducing waste, recycling materials, and minimizing energy consumption during production.
VII. Conclusion
In summary, the production processes for metal resistors are complex and multifaceted, involving various types of resistors, raw materials, and fabrication techniques. Understanding these processes is crucial for appreciating the role of resistors in electronic circuits and the advancements being made in the field. As technology continues to evolve, the future of metal resistors looks promising, with innovations in materials science, automation, and sustainability paving the way for enhanced performance and reliability in electronic applications.