Latest Manufacturing Processes for Resistor Resistance
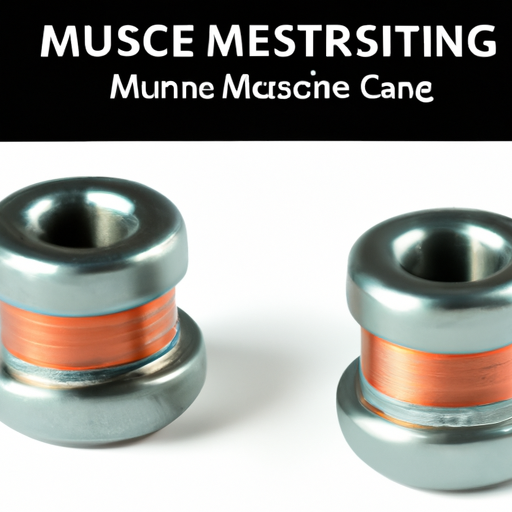
I. Introduction
Resistors are fundamental components in electronic circuits, serving the critical function of controlling current flow. They are essential for protecting sensitive components, dividing voltages, and setting bias points in various applications. Over the years, the manufacturing processes for resistors have evolved significantly, driven by advancements in technology and materials. This article aims to explore the latest manufacturing processes for resistor resistance, highlighting innovations that enhance performance, reliability, and sustainability.
II. Types of Resistors
Resistors come in various types, each designed for specific applications. Understanding these types is crucial for appreciating the advancements in their manufacturing processes.
A. Fixed Resistors
1. **Carbon Composition Resistors**: These resistors are made from a mixture of carbon particles and a binding resin. They are known for their high energy absorption but have largely been replaced by more stable options.
2. **Film Resistors**: This category includes carbon film and metal film resistors. They are produced by depositing a thin layer of resistive material onto a substrate. Metal film resistors, in particular, offer better stability and lower noise.
3. **Wirewound Resistors**: Made by winding a metal wire around a ceramic or fiberglass core, these resistors can handle high power levels and are often used in high-precision applications.
B. Variable Resistors
1. **Potentiometers**: These resistors allow for adjustable resistance and are commonly used in volume controls and tuning circuits.
2. **Rheostats**: Similar to potentiometers but designed to handle higher currents, rheostats are used for adjusting current flow in circuits.
C. Specialty Resistors
1. **Thermistors**: Temperature-sensitive resistors that change resistance with temperature variations, thermistors are widely used in temperature sensing applications.
2. **Photoresistors**: Also known as light-dependent resistors (LDRs), these components change resistance based on light exposure, making them useful in light-sensing applications.
III. Traditional Manufacturing Processes
Historically, resistor manufacturing relied on methods that have now become outdated.
A. Overview of Historical Methods
1. **Carbon Composition Mixing**: This method involved mixing carbon with a binder and shaping it into resistors. While effective, it resulted in significant variability in resistance values.
2. **Wirewound Techniques**: Although still in use, traditional wirewound techniques often led to larger resistor sizes and limited design flexibility.
B. Limitations of Traditional Processes
1. **Tolerance and Stability Issues**: Traditional methods often resulted in resistors with poor tolerance levels, leading to inconsistent performance in circuits.
2. **Environmental Concerns**: The materials and processes used in traditional manufacturing raised environmental concerns, prompting the industry to seek more sustainable alternatives.
IV. Latest Manufacturing Technologies
Recent advancements in manufacturing technologies have revolutionized resistor production, enhancing precision and performance.
A. Thin Film Technology
Thin film technology involves depositing a very thin layer of resistive material onto a substrate. This process allows for precise control over resistance values and results in resistors with excellent stability and low noise.
**Advantages**: Thin film resistors are known for their high precision, stability, and miniaturization capabilities, making them ideal for modern electronic applications.
B. Thick Film Technology
Thick film technology, on the other hand, involves printing a thicker layer of resistive material onto a substrate. This method is more cost-effective and versatile, allowing for the production of a wide range of resistor types.
**Advantages**: Thick film resistors are less expensive to produce and can be manufactured in various shapes and sizes, making them suitable for diverse applications.
C. Laser Trimming Techniques
Laser trimming is a process that fine-tunes the resistance value of a resistor after it has been manufactured. By using a laser to remove material, manufacturers can achieve precise resistance values.
**Benefits**: This technique improves accuracy and allows for the customization of resistors to meet specific circuit requirements.
D. 3D Printing in Resistor Manufacturing
Additive manufacturing, or 3D printing, is emerging as a novel approach in resistor production. This technology allows for the creation of complex resistor geometries that were previously impossible to achieve.
**Potential Applications and Benefits**: 3D printing can lead to significant reductions in material waste and enable the production of highly customized resistors for niche applications.
V. Advanced Materials in Resistor Manufacturing
The development of new materials has also played a crucial role in enhancing resistor performance.
A. Conductive Polymers
Conductive polymers are organic compounds that conduct electricity. They offer unique properties, such as flexibility and lightweight, making them suitable for various applications.
**Applications in Modern Resistors**: These materials are increasingly used in flexible electronics and wearable devices, where traditional resistors may not be practical.
B. Nanomaterials
Nanomaterials, including carbon nanotubes and graphene, have gained attention for their exceptional electrical properties. These materials can significantly enhance the performance of resistors.
**Impact on Performance and Miniaturization**: The use of nanomaterials allows for the production of smaller, more efficient resistors with improved thermal stability and conductivity.
C. Metal Oxides
Metal oxides are commonly used in high-temperature and high-power resistors. They offer excellent stability and reliability, making them suitable for demanding applications.
**Advantages in Stability and Reliability**: Resistors made from metal oxides can withstand extreme conditions, ensuring consistent performance in critical applications.
VI. Quality Control and Testing
Quality assurance is paramount in resistor manufacturing to ensure reliability and performance.
A. Importance of Quality Assurance
Manufacturers must adhere to strict quality control measures to guarantee that resistors meet industry standards and customer expectations.
B. Latest Testing Methods
1. **Automated Testing Systems**: Automation in testing processes enhances efficiency and accuracy, allowing for rapid assessment of resistor performance.
2. **Environmental Testing for Reliability**: Resistors are subjected to various environmental conditions to ensure they can withstand real-world applications.
C. Standards and Certifications
Compliance with industry standards and certifications is essential for manufacturers to demonstrate the quality and reliability of their products.
VII. Environmental Considerations
As the electronics industry evolves, so does the need for sustainable manufacturing practices.
A. Sustainable Manufacturing Practices
Manufacturers are increasingly adopting eco-friendly practices, such as reducing waste and using recyclable materials in resistor production.
B. Recycling and Disposal of Resistors
Proper recycling and disposal methods are crucial to minimize environmental impact. Many manufacturers are exploring ways to reclaim materials from old resistors.
C. Compliance with Environmental Regulations
Adhering to environmental regulations is essential for manufacturers to ensure their processes are sustainable and responsible.
VIII. Future Trends in Resistor Manufacturing
The future of resistor manufacturing is poised for exciting developments.
A. Integration with Smart Technologies
As the demand for smart devices grows, resistors will increasingly be integrated into smart technologies, enhancing their functionality and performance.
B. Miniaturization and the Internet of Things (IoT)
The trend toward miniaturization will continue, driven by the proliferation of IoT devices that require compact and efficient components.
C. Potential for New Materials and Processes
Ongoing research into new materials and manufacturing processes will likely lead to further innovations in resistor technology, improving performance and sustainability.
IX. Conclusion
The manufacturing processes for resistor resistance have come a long way, evolving from traditional methods to advanced technologies that enhance precision, reliability, and sustainability. As the electronics industry continues to innovate, the importance of resistors remains steadfast. The future of resistor manufacturing promises exciting developments, driven by advancements in materials and processes that will shape the next generation of electronic devices.
X. References
A comprehensive list of academic papers, articles, and industry reports would be included here to support the research and claims made in this article.
---
This blog post provides an in-depth exploration of the latest manufacturing processes for resistor resistance, covering various aspects from types of resistors to future trends in the industry. Each section is designed to inform and educate readers about the advancements in resistor technology.
Latest Manufacturing Processes for Resistor Resistance
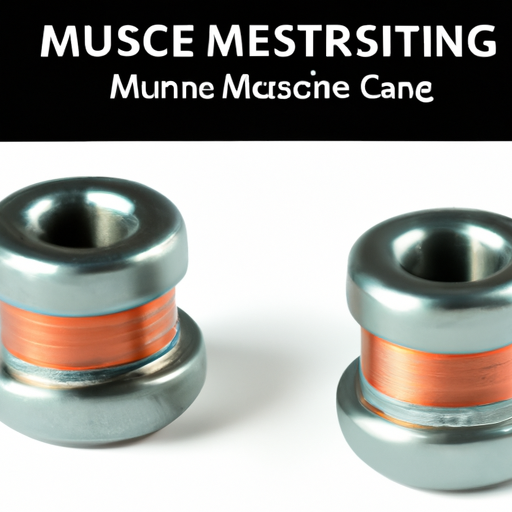
I. Introduction
Resistors are fundamental components in electronic circuits, serving the critical function of controlling current flow. They are essential for protecting sensitive components, dividing voltages, and setting bias points in various applications. Over the years, the manufacturing processes for resistors have evolved significantly, driven by advancements in technology and materials. This article aims to explore the latest manufacturing processes for resistor resistance, highlighting innovations that enhance performance, reliability, and sustainability.
II. Types of Resistors
Resistors come in various types, each designed for specific applications. Understanding these types is crucial for appreciating the advancements in their manufacturing processes.
A. Fixed Resistors
1. **Carbon Composition Resistors**: These resistors are made from a mixture of carbon particles and a binding resin. They are known for their high energy absorption but have largely been replaced by more stable options.
2. **Film Resistors**: This category includes carbon film and metal film resistors. They are produced by depositing a thin layer of resistive material onto a substrate. Metal film resistors, in particular, offer better stability and lower noise.
3. **Wirewound Resistors**: Made by winding a metal wire around a ceramic or fiberglass core, these resistors can handle high power levels and are often used in high-precision applications.
B. Variable Resistors
1. **Potentiometers**: These resistors allow for adjustable resistance and are commonly used in volume controls and tuning circuits.
2. **Rheostats**: Similar to potentiometers but designed to handle higher currents, rheostats are used for adjusting current flow in circuits.
C. Specialty Resistors
1. **Thermistors**: Temperature-sensitive resistors that change resistance with temperature variations, thermistors are widely used in temperature sensing applications.
2. **Photoresistors**: Also known as light-dependent resistors (LDRs), these components change resistance based on light exposure, making them useful in light-sensing applications.
III. Traditional Manufacturing Processes
Historically, resistor manufacturing relied on methods that have now become outdated.
A. Overview of Historical Methods
1. **Carbon Composition Mixing**: This method involved mixing carbon with a binder and shaping it into resistors. While effective, it resulted in significant variability in resistance values.
2. **Wirewound Techniques**: Although still in use, traditional wirewound techniques often led to larger resistor sizes and limited design flexibility.
B. Limitations of Traditional Processes
1. **Tolerance and Stability Issues**: Traditional methods often resulted in resistors with poor tolerance levels, leading to inconsistent performance in circuits.
2. **Environmental Concerns**: The materials and processes used in traditional manufacturing raised environmental concerns, prompting the industry to seek more sustainable alternatives.
IV. Latest Manufacturing Technologies
Recent advancements in manufacturing technologies have revolutionized resistor production, enhancing precision and performance.
A. Thin Film Technology
Thin film technology involves depositing a very thin layer of resistive material onto a substrate. This process allows for precise control over resistance values and results in resistors with excellent stability and low noise.
**Advantages**: Thin film resistors are known for their high precision, stability, and miniaturization capabilities, making them ideal for modern electronic applications.
B. Thick Film Technology
Thick film technology, on the other hand, involves printing a thicker layer of resistive material onto a substrate. This method is more cost-effective and versatile, allowing for the production of a wide range of resistor types.
**Advantages**: Thick film resistors are less expensive to produce and can be manufactured in various shapes and sizes, making them suitable for diverse applications.
C. Laser Trimming Techniques
Laser trimming is a process that fine-tunes the resistance value of a resistor after it has been manufactured. By using a laser to remove material, manufacturers can achieve precise resistance values.
**Benefits**: This technique improves accuracy and allows for the customization of resistors to meet specific circuit requirements.
D. 3D Printing in Resistor Manufacturing
Additive manufacturing, or 3D printing, is emerging as a novel approach in resistor production. This technology allows for the creation of complex resistor geometries that were previously impossible to achieve.
**Potential Applications and Benefits**: 3D printing can lead to significant reductions in material waste and enable the production of highly customized resistors for niche applications.
V. Advanced Materials in Resistor Manufacturing
The development of new materials has also played a crucial role in enhancing resistor performance.
A. Conductive Polymers
Conductive polymers are organic compounds that conduct electricity. They offer unique properties, such as flexibility and lightweight, making them suitable for various applications.
**Applications in Modern Resistors**: These materials are increasingly used in flexible electronics and wearable devices, where traditional resistors may not be practical.
B. Nanomaterials
Nanomaterials, including carbon nanotubes and graphene, have gained attention for their exceptional electrical properties. These materials can significantly enhance the performance of resistors.
**Impact on Performance and Miniaturization**: The use of nanomaterials allows for the production of smaller, more efficient resistors with improved thermal stability and conductivity.
C. Metal Oxides
Metal oxides are commonly used in high-temperature and high-power resistors. They offer excellent stability and reliability, making them suitable for demanding applications.
**Advantages in Stability and Reliability**: Resistors made from metal oxides can withstand extreme conditions, ensuring consistent performance in critical applications.
VI. Quality Control and Testing
Quality assurance is paramount in resistor manufacturing to ensure reliability and performance.
A. Importance of Quality Assurance
Manufacturers must adhere to strict quality control measures to guarantee that resistors meet industry standards and customer expectations.
B. Latest Testing Methods
1. **Automated Testing Systems**: Automation in testing processes enhances efficiency and accuracy, allowing for rapid assessment of resistor performance.
2. **Environmental Testing for Reliability**: Resistors are subjected to various environmental conditions to ensure they can withstand real-world applications.
C. Standards and Certifications
Compliance with industry standards and certifications is essential for manufacturers to demonstrate the quality and reliability of their products.
VII. Environmental Considerations
As the electronics industry evolves, so does the need for sustainable manufacturing practices.
A. Sustainable Manufacturing Practices
Manufacturers are increasingly adopting eco-friendly practices, such as reducing waste and using recyclable materials in resistor production.
B. Recycling and Disposal of Resistors
Proper recycling and disposal methods are crucial to minimize environmental impact. Many manufacturers are exploring ways to reclaim materials from old resistors.
C. Compliance with Environmental Regulations
Adhering to environmental regulations is essential for manufacturers to ensure their processes are sustainable and responsible.
VIII. Future Trends in Resistor Manufacturing
The future of resistor manufacturing is poised for exciting developments.
A. Integration with Smart Technologies
As the demand for smart devices grows, resistors will increasingly be integrated into smart technologies, enhancing their functionality and performance.
B. Miniaturization and the Internet of Things (IoT)
The trend toward miniaturization will continue, driven by the proliferation of IoT devices that require compact and efficient components.
C. Potential for New Materials and Processes
Ongoing research into new materials and manufacturing processes will likely lead to further innovations in resistor technology, improving performance and sustainability.
IX. Conclusion
The manufacturing processes for resistor resistance have come a long way, evolving from traditional methods to advanced technologies that enhance precision, reliability, and sustainability. As the electronics industry continues to innovate, the importance of resistors remains steadfast. The future of resistor manufacturing promises exciting developments, driven by advancements in materials and processes that will shape the next generation of electronic devices.
X. References
A comprehensive list of academic papers, articles, and industry reports would be included here to support the research and claims made in this article.
---
This blog post provides an in-depth exploration of the latest manufacturing processes for resistor resistance, covering various aspects from types of resistors to future trends in the industry. Each section is designed to inform and educate readers about the advancements in resistor technology.