What are the Product Standards for Resistor Packaging?
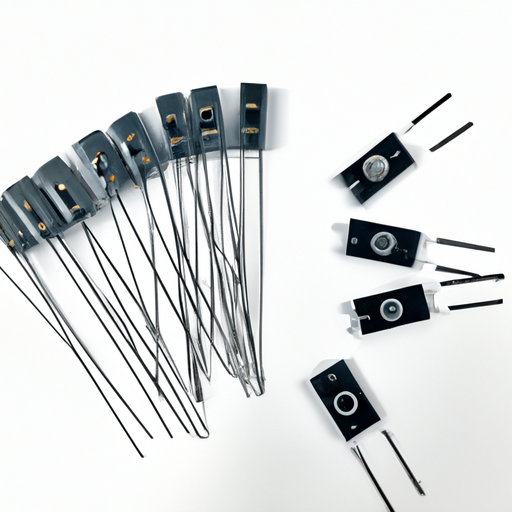
I. Introduction
Resistors are fundamental components in electronic circuits, serving the critical function of controlling current flow and voltage levels. Their importance cannot be overstated, as they are integral to the operation of virtually all electronic devices, from simple household appliances to complex computing systems. However, the performance and reliability of resistors are not solely determined by their electrical characteristics; the packaging in which they are housed plays a significant role as well. This article aims to explore the product standards for resistor packaging, shedding light on the various types, materials, regulatory guidelines, performance specifications, and industry trends that shape this essential aspect of electronic components.
II. Understanding Resistor Packaging
A. Types of Resistor Packaging
Resistor packaging comes in several forms, each designed to meet specific application requirements:
1. **Through-hole Resistors**: These resistors are designed for insertion into holes on a printed circuit board (PCB). They are typically larger and provide robust mechanical support, making them suitable for applications where durability is essential.
2. **Surface-mount Resistors**: These resistors are mounted directly onto the surface of a PCB, allowing for a more compact design. They are widely used in modern electronics due to their space-saving advantages and compatibility with automated assembly processes.
3. **Chip Resistors**: A subtype of surface-mount resistors, chip resistors are small, rectangular components that are ideal for high-density applications. Their minimal size and weight make them popular in mobile devices and other compact electronics.
B. Materials Used in Resistor Packaging
The materials used in resistor packaging significantly influence their performance and reliability:
1. **Ceramic**: Often used for high-power resistors, ceramic materials provide excellent thermal stability and electrical insulation. They are resistant to high temperatures and environmental factors, making them suitable for demanding applications.
2. **Plastic**: Commonly used for lower-cost resistors, plastic packaging is lightweight and can be molded into various shapes. However, it may not offer the same level of thermal performance as ceramic.
3. **Metal**: Metal packaging is typically used for precision resistors that require high durability and thermal conductivity. Metal can effectively dissipate heat, making it ideal for high-power applications.
C. Importance of Packaging in Thermal Management and Electrical Performance
The packaging of resistors is crucial for thermal management, as it affects how heat is dissipated during operation. Proper thermal management ensures that resistors operate within their specified temperature ranges, preventing failure and extending their lifespan. Additionally, the packaging influences electrical performance, including resistance stability and noise characteristics, which are vital for maintaining signal integrity in electronic circuits.
III. Regulatory Standards and Guidelines
A. International Standards Organizations
Several international organizations establish standards that govern resistor packaging:
1. **International Electrotechnical Commission (IEC)**: The IEC develops international standards for electrical and electronic technologies, including those related to resistors.
2. **Institute of Electrical and Electronics Engineers (IEEE)**: IEEE standards cover a wide range of electrical and electronic components, providing guidelines for performance and testing.
3. **American National Standards Institute (ANSI)**: ANSI oversees the development of voluntary consensus standards for various industries, including electronics.
B. Key Standards Relevant to Resistor Packaging
1. **IEC 60115**: This standard specifies requirements for fixed resistors used in electronic equipment, covering aspects such as electrical characteristics, mechanical properties, and environmental performance.
2. **IPC Standards for Electronic Packaging**: The IPC (Institute for Printed Circuits) provides standards for the design and manufacturing of electronic assemblies, including guidelines for resistor packaging.
3. **RoHS Compliance**: The Restriction of Hazardous Substances (RoHS) directive mandates the reduction of hazardous materials in electronic products, influencing the materials and processes used in resistor packaging.
IV. Performance Specifications
A. Electrical Characteristics
1. **Resistance Tolerance**: This specification indicates the allowable deviation from the nominal resistance value. High-precision applications may require tighter tolerances.
2. **Temperature Coefficient**: This parameter measures how much the resistance changes with temperature. A low temperature coefficient is desirable for applications requiring stable performance across varying temperatures.
3. **Power Rating**: The power rating indicates the maximum power a resistor can dissipate without overheating. Proper packaging is essential to ensure that resistors can handle their rated power.
B. Mechanical Characteristics
1. **Size and Dimensions**: The physical size of resistors affects their mounting options and compatibility with PCBs. Standards dictate the dimensions for various resistor types.
2. **Mounting Compatibility**: Resistor packaging must be compatible with the mounting techniques used in PCB assembly, whether through-hole or surface-mount.
3. **Durability and Mechanical Stress Resistance**: Resistors must withstand mechanical stresses during handling and operation. Packaging materials and designs are critical in ensuring durability.
C. Thermal Characteristics
1. **Thermal Resistance**: This specification measures how effectively a resistor can dissipate heat. Lower thermal resistance is preferable for high-power applications.
2. **Heat Dissipation Capabilities**: Effective heat dissipation is vital for maintaining performance and reliability. Packaging designs must facilitate adequate airflow and heat transfer.
V. Quality Assurance and Testing
A. Importance of Quality Assurance in Resistor Packaging
Quality assurance is essential in ensuring that resistors meet established standards and perform reliably in their intended applications. Rigorous testing and certification processes help manufacturers maintain high-quality products.
B. Common Testing Methods
1. **Visual Inspection**: This initial step involves checking for physical defects, such as cracks or improper markings, that could affect performance.
2. **Electrical Testing**: Resistors undergo electrical testing to verify their resistance values, tolerances, and other electrical characteristics.
3. **Environmental Testing**: Resistors are subjected to various environmental conditions, such as temperature and humidity, to assess their performance under real-world conditions.
C. Certification Processes and Third-Party Testing
Many manufacturers seek certification from recognized organizations to validate their products' compliance with industry standards. Third-party testing provides an additional layer of assurance, ensuring that resistors meet the required specifications.
VI. Industry Trends and Innovations
A. Advances in Materials and Manufacturing Processes
The electronics industry is witnessing continuous advancements in materials and manufacturing processes, leading to improved resistor packaging. Innovations such as nanomaterials and advanced ceramics enhance thermal and electrical performance.
B. Miniaturization and Its Impact on Packaging Standards
As electronic devices become smaller and more compact, the demand for miniaturized resistors increases. This trend necessitates the development of new packaging standards that accommodate smaller sizes while maintaining performance and reliability.
C. The Role of Automation and Smart Technologies in Resistor Packaging
Automation and smart technologies are revolutionizing the manufacturing and testing of resistors. Automated assembly processes improve efficiency and consistency, while smart technologies enable real-time monitoring of resistor performance during production.
VII. Challenges in Resistor Packaging
A. Balancing Performance and Cost
Manufacturers face the challenge of balancing performance with cost. While high-quality materials and advanced packaging designs can enhance performance, they may also increase production costs.
B. Addressing Environmental Concerns and Sustainability
As environmental concerns grow, the electronics industry must adapt to sustainability requirements. This includes using eco-friendly materials and processes in resistor packaging to comply with regulations like RoHS.
C. Adapting to Rapid Technological Changes in the Electronics Industry
The fast-paced nature of the electronics industry requires resistor manufacturers to stay ahead of technological changes. This includes adapting packaging standards to accommodate new applications and emerging technologies.
VIII. Conclusion
In conclusion, product standards for resistor packaging are vital for ensuring the performance, reliability, and safety of electronic components. As technology continues to evolve, so too will the standards that govern resistor packaging. Manufacturers must remain vigilant in adhering to established guidelines while embracing innovations that enhance product quality. The future of resistor packaging will likely see a continued focus on miniaturization, sustainability, and advanced materials, all of which will play a crucial role in shaping the next generation of electronic devices.
IX. References
1. International Electrotechnical Commission (IEC). (n.d.). IEC 60115 - Fixed resistors for use in electronic equipment.
2. IPC. (n.d.). IPC Standards for Electronic Packaging.
3. European Commission. (n.d.). RoHS Compliance and Environmental Considerations.
4. IEEE Standards Association. (n.d.). Institute of Electrical and Electronics Engineers (IEEE) Standards.
5. Various academic and industry publications on resistor packaging and electronic component standards.
What are the Product Standards for Resistor Packaging?
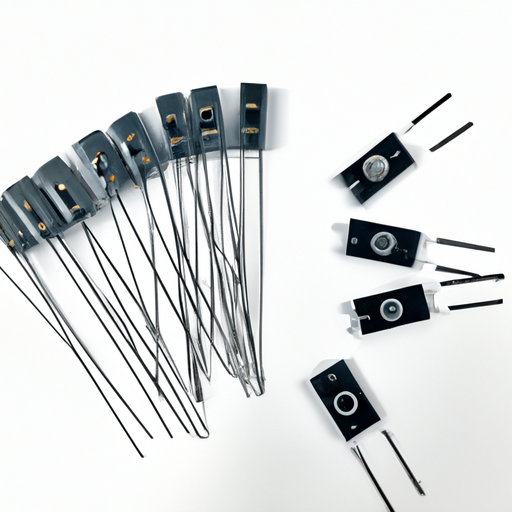
I. Introduction
Resistors are fundamental components in electronic circuits, serving the critical function of controlling current flow and voltage levels. Their importance cannot be overstated, as they are integral to the operation of virtually all electronic devices, from simple household appliances to complex computing systems. However, the performance and reliability of resistors are not solely determined by their electrical characteristics; the packaging in which they are housed plays a significant role as well. This article aims to explore the product standards for resistor packaging, shedding light on the various types, materials, regulatory guidelines, performance specifications, and industry trends that shape this essential aspect of electronic components.
II. Understanding Resistor Packaging
A. Types of Resistor Packaging
Resistor packaging comes in several forms, each designed to meet specific application requirements:
1. **Through-hole Resistors**: These resistors are designed for insertion into holes on a printed circuit board (PCB). They are typically larger and provide robust mechanical support, making them suitable for applications where durability is essential.
2. **Surface-mount Resistors**: These resistors are mounted directly onto the surface of a PCB, allowing for a more compact design. They are widely used in modern electronics due to their space-saving advantages and compatibility with automated assembly processes.
3. **Chip Resistors**: A subtype of surface-mount resistors, chip resistors are small, rectangular components that are ideal for high-density applications. Their minimal size and weight make them popular in mobile devices and other compact electronics.
B. Materials Used in Resistor Packaging
The materials used in resistor packaging significantly influence their performance and reliability:
1. **Ceramic**: Often used for high-power resistors, ceramic materials provide excellent thermal stability and electrical insulation. They are resistant to high temperatures and environmental factors, making them suitable for demanding applications.
2. **Plastic**: Commonly used for lower-cost resistors, plastic packaging is lightweight and can be molded into various shapes. However, it may not offer the same level of thermal performance as ceramic.
3. **Metal**: Metal packaging is typically used for precision resistors that require high durability and thermal conductivity. Metal can effectively dissipate heat, making it ideal for high-power applications.
C. Importance of Packaging in Thermal Management and Electrical Performance
The packaging of resistors is crucial for thermal management, as it affects how heat is dissipated during operation. Proper thermal management ensures that resistors operate within their specified temperature ranges, preventing failure and extending their lifespan. Additionally, the packaging influences electrical performance, including resistance stability and noise characteristics, which are vital for maintaining signal integrity in electronic circuits.
III. Regulatory Standards and Guidelines
A. International Standards Organizations
Several international organizations establish standards that govern resistor packaging:
1. **International Electrotechnical Commission (IEC)**: The IEC develops international standards for electrical and electronic technologies, including those related to resistors.
2. **Institute of Electrical and Electronics Engineers (IEEE)**: IEEE standards cover a wide range of electrical and electronic components, providing guidelines for performance and testing.
3. **American National Standards Institute (ANSI)**: ANSI oversees the development of voluntary consensus standards for various industries, including electronics.
B. Key Standards Relevant to Resistor Packaging
1. **IEC 60115**: This standard specifies requirements for fixed resistors used in electronic equipment, covering aspects such as electrical characteristics, mechanical properties, and environmental performance.
2. **IPC Standards for Electronic Packaging**: The IPC (Institute for Printed Circuits) provides standards for the design and manufacturing of electronic assemblies, including guidelines for resistor packaging.
3. **RoHS Compliance**: The Restriction of Hazardous Substances (RoHS) directive mandates the reduction of hazardous materials in electronic products, influencing the materials and processes used in resistor packaging.
IV. Performance Specifications
A. Electrical Characteristics
1. **Resistance Tolerance**: This specification indicates the allowable deviation from the nominal resistance value. High-precision applications may require tighter tolerances.
2. **Temperature Coefficient**: This parameter measures how much the resistance changes with temperature. A low temperature coefficient is desirable for applications requiring stable performance across varying temperatures.
3. **Power Rating**: The power rating indicates the maximum power a resistor can dissipate without overheating. Proper packaging is essential to ensure that resistors can handle their rated power.
B. Mechanical Characteristics
1. **Size and Dimensions**: The physical size of resistors affects their mounting options and compatibility with PCBs. Standards dictate the dimensions for various resistor types.
2. **Mounting Compatibility**: Resistor packaging must be compatible with the mounting techniques used in PCB assembly, whether through-hole or surface-mount.
3. **Durability and Mechanical Stress Resistance**: Resistors must withstand mechanical stresses during handling and operation. Packaging materials and designs are critical in ensuring durability.
C. Thermal Characteristics
1. **Thermal Resistance**: This specification measures how effectively a resistor can dissipate heat. Lower thermal resistance is preferable for high-power applications.
2. **Heat Dissipation Capabilities**: Effective heat dissipation is vital for maintaining performance and reliability. Packaging designs must facilitate adequate airflow and heat transfer.
V. Quality Assurance and Testing
A. Importance of Quality Assurance in Resistor Packaging
Quality assurance is essential in ensuring that resistors meet established standards and perform reliably in their intended applications. Rigorous testing and certification processes help manufacturers maintain high-quality products.
B. Common Testing Methods
1. **Visual Inspection**: This initial step involves checking for physical defects, such as cracks or improper markings, that could affect performance.
2. **Electrical Testing**: Resistors undergo electrical testing to verify their resistance values, tolerances, and other electrical characteristics.
3. **Environmental Testing**: Resistors are subjected to various environmental conditions, such as temperature and humidity, to assess their performance under real-world conditions.
C. Certification Processes and Third-Party Testing
Many manufacturers seek certification from recognized organizations to validate their products' compliance with industry standards. Third-party testing provides an additional layer of assurance, ensuring that resistors meet the required specifications.
VI. Industry Trends and Innovations
A. Advances in Materials and Manufacturing Processes
The electronics industry is witnessing continuous advancements in materials and manufacturing processes, leading to improved resistor packaging. Innovations such as nanomaterials and advanced ceramics enhance thermal and electrical performance.
B. Miniaturization and Its Impact on Packaging Standards
As electronic devices become smaller and more compact, the demand for miniaturized resistors increases. This trend necessitates the development of new packaging standards that accommodate smaller sizes while maintaining performance and reliability.
C. The Role of Automation and Smart Technologies in Resistor Packaging
Automation and smart technologies are revolutionizing the manufacturing and testing of resistors. Automated assembly processes improve efficiency and consistency, while smart technologies enable real-time monitoring of resistor performance during production.
VII. Challenges in Resistor Packaging
A. Balancing Performance and Cost
Manufacturers face the challenge of balancing performance with cost. While high-quality materials and advanced packaging designs can enhance performance, they may also increase production costs.
B. Addressing Environmental Concerns and Sustainability
As environmental concerns grow, the electronics industry must adapt to sustainability requirements. This includes using eco-friendly materials and processes in resistor packaging to comply with regulations like RoHS.
C. Adapting to Rapid Technological Changes in the Electronics Industry
The fast-paced nature of the electronics industry requires resistor manufacturers to stay ahead of technological changes. This includes adapting packaging standards to accommodate new applications and emerging technologies.
VIII. Conclusion
In conclusion, product standards for resistor packaging are vital for ensuring the performance, reliability, and safety of electronic components. As technology continues to evolve, so too will the standards that govern resistor packaging. Manufacturers must remain vigilant in adhering to established guidelines while embracing innovations that enhance product quality. The future of resistor packaging will likely see a continued focus on miniaturization, sustainability, and advanced materials, all of which will play a crucial role in shaping the next generation of electronic devices.
IX. References
1. International Electrotechnical Commission (IEC). (n.d.). IEC 60115 - Fixed resistors for use in electronic equipment.
2. IPC. (n.d.). IPC Standards for Electronic Packaging.
3. European Commission. (n.d.). RoHS Compliance and Environmental Considerations.
4. IEEE Standards Association. (n.d.). Institute of Electrical and Electronics Engineers (IEEE) Standards.
5. Various academic and industry publications on resistor packaging and electronic component standards.