What is the Mainstream Ceramic Capacitor Production Process?
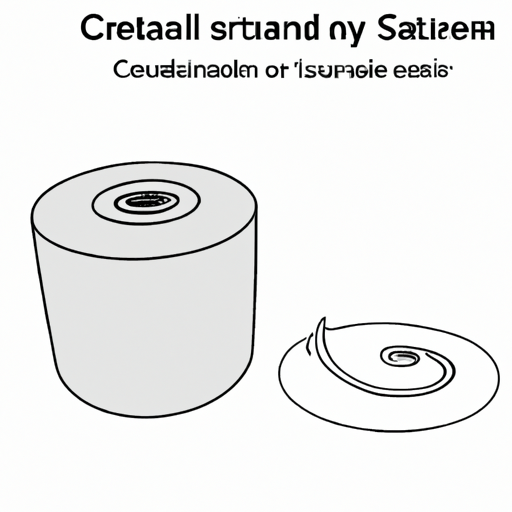
I. Introduction
A. Definition of Ceramic Capacitors
Ceramic capacitors are passive electronic components that store electrical energy in an electric field. They are made from ceramic materials, which are non-metallic and inorganic, and are widely used in various electronic circuits due to their reliability and stability. These capacitors are characterized by their ability to maintain capacitance over a wide range of temperatures and voltages.
B. Importance of Ceramic Capacitors in Electronics
Ceramic capacitors play a crucial role in modern electronics. They are used in applications ranging from filtering and decoupling to timing and energy storage. Their small size, low cost, and high reliability make them ideal for use in consumer electronics, automotive systems, telecommunications, and industrial equipment. As technology advances, the demand for efficient and compact capacitors continues to grow, further emphasizing the importance of ceramic capacitors in the electronics industry.
C. Overview of the Production Process
The production of ceramic capacitors involves several key steps, including material preparation, forming, drying, sintering, electrode application, and final finishing. Each stage is critical to ensuring the quality and performance of the final product. This blog post will delve into the mainstream production process of ceramic capacitors, exploring the materials used, the techniques employed, and the challenges faced by manufacturers.
II. Types of Ceramic Capacitors
A. Class 1 Capacitors
1. Characteristics
Class 1 ceramic capacitors are known for their stability and low loss characteristics. They typically have a dielectric constant of less than 100 and exhibit minimal capacitance change with temperature and voltage variations. This makes them suitable for precision applications.
2. Applications
These capacitors are commonly used in timing circuits, oscillators, and RF applications where stability is paramount.
B. Class 2 Capacitors
1. Characteristics
Class 2 ceramic capacitors have a higher dielectric constant, which allows for greater capacitance in a smaller package. However, they are less stable than Class 1 capacitors, with capacitance values that can vary significantly with temperature and voltage.
2. Applications
Class 2 capacitors are widely used in applications such as decoupling, filtering, and energy storage in power supply circuits.
C. Comparison of Class 1 and Class 2 Capacitors
While Class 1 capacitors are preferred for applications requiring high stability and low loss, Class 2 capacitors are favored for their higher capacitance values and smaller sizes. The choice between the two depends on the specific requirements of the electronic circuit.
III. Raw Materials
A. Types of Ceramic Materials
1. Barium Titanate
Barium titanate (BaTiO3) is the most commonly used dielectric material in ceramic capacitors. It has a high dielectric constant and excellent temperature stability, making it ideal for Class 2 capacitors.
2. Other Materials
Other ceramic materials, such as strontium titanate and lead zirconate titanate, are also used in specific applications, particularly where unique electrical properties are required.
B. Conductive Materials
1. Silver
Silver is the most widely used conductive material for the electrodes of ceramic capacitors due to its excellent conductivity and reliability.
2. Other Metal Oxides
In some cases, other metal oxides, such as nickel or palladium, may be used as alternatives to silver, particularly in cost-sensitive applications.
C. Additives and Their Functions
Additives are often included in the ceramic mixture to enhance specific properties, such as improving sintering behavior, increasing dielectric strength, or modifying the thermal expansion coefficient.
IV. The Production Process
A. Material Preparation
1. Sourcing and Quality Control
The production process begins with sourcing high-quality raw materials. Manufacturers must ensure that the materials meet strict quality standards to achieve the desired electrical properties in the final product.
2. Mixing and Milling
Once the materials are sourced, they are mixed and milled to create a homogeneous powder. This step is crucial, as uneven mixing can lead to inconsistencies in the final product.
B. Forming
1. Methods of Forming
There are several methods for forming ceramic capacitors, including:
Tape Casting: A thin layer of the ceramic mixture is spread onto a substrate and then cut into desired shapes.
Pressing: The ceramic powder is compacted into molds under high pressure to form the capacitor body.
Injection Molding: The ceramic mixture is injected into molds to create complex shapes.
2. Importance of Forming Techniques
The choice of forming technique can significantly impact the density and uniformity of the capacitor, which in turn affects its electrical performance.
C. Drying
1. Purpose of Drying
After forming, the capacitors must be dried to remove any moisture that could affect the sintering process. Proper drying is essential to prevent defects such as cracking or warping.
2. Techniques Used
Common drying techniques include air drying and forced drying in ovens, with careful control of temperature and humidity to ensure uniform drying.
D. Sintering
1. Definition and Importance
Sintering is the process of heating the dried ceramic body to a temperature below its melting point, causing the particles to bond together. This step is critical for achieving the desired mechanical strength and electrical properties.
2. Sintering Process
Temperature Control: The sintering temperature must be carefully controlled to ensure optimal bonding without causing excessive shrinkage or deformation.
Atmosphere Control: The atmosphere in the sintering furnace can also affect the properties of the ceramic. Inert or reducing atmospheres are often used to prevent oxidation of the materials.
E. Electrode Application
1. Methods of Electrode Application
Electrodes are applied to the ceramic body using various methods, including:
Screen Printing: A paste containing conductive materials is printed onto the ceramic surface.
Vapor Deposition: A thin layer of conductive material is deposited onto the ceramic using vapor deposition techniques.
2. Importance of Electrode Quality
The quality of the electrodes is crucial for the overall performance of the capacitor. Poorly applied electrodes can lead to increased resistance and reduced capacitance.
F. Final Finishing
1. Trimming and Testing
After electrode application, the capacitors are trimmed to the desired size and undergo rigorous testing to ensure they meet electrical specifications.
2. Coating and Packaging
Finally, the capacitors are coated for protection and packaged for shipment. Proper packaging is essential to prevent damage during transportation and storage.
V. Quality Control
A. Testing Methods
1. Electrical Testing
Electrical testing is conducted to measure capacitance, dissipation factor, and insulation resistance. These tests ensure that the capacitors meet industry standards.
2. Mechanical Testing
Mechanical testing assesses the physical integrity of the capacitors, including their resistance to mechanical stress and thermal cycling.
B. Standards and Certifications
1. Industry Standards
Manufacturers must adhere to various industry standards, such as those set by the International Electrotechnical Commission (IEC) and the American National Standards Institute (ANSI), to ensure product quality and safety.
2. Environmental Considerations
Environmental regulations also play a role in the production process, with manufacturers required to minimize waste and emissions.
VI. Challenges in Production
A. Material Sourcing Issues
Sourcing high-quality raw materials can be challenging, particularly in a global market where supply chain disruptions can occur.
B. Technological Advancements
As technology evolves, manufacturers must continuously adapt their production processes to incorporate new materials and techniques, which can be both costly and time-consuming.
C. Environmental Impact and Sustainability
The production of ceramic capacitors can have environmental impacts, including waste generation and energy consumption. Manufacturers are increasingly focusing on sustainable practices to mitigate these effects.
VII. Future Trends in Ceramic Capacitor Production
A. Innovations in Materials
Research is ongoing into new ceramic materials that offer improved performance characteristics, such as higher capacitance and better thermal stability.
B. Advances in Production Techniques
Automation and advanced manufacturing techniques, such as 3D printing, are being explored to enhance production efficiency and reduce costs.
C. Market Demand and Growth Projections
The demand for ceramic capacitors is expected to grow, driven by advancements in technology and the increasing use of electronic devices in various industries.
VIII. Conclusion
A. Summary of the Production Process
The production of ceramic capacitors involves a complex series of steps, from material preparation to final finishing. Each stage is critical to ensuring the quality and performance of the final product.
B. Importance of Continuous Improvement
As the electronics industry continues to evolve, manufacturers must prioritize continuous improvement in their production processes to meet changing demands and maintain competitiveness.
C. The Role of Ceramic Capacitors in Future Technologies
Ceramic capacitors will continue to play a vital role in the development of future technologies, supporting innovations in consumer electronics, renewable energy, and beyond.
IX. References
A. Academic Journals
- Journal of Materials Science
- IEEE Transactions on Electronics Packaging Manufacturing
B. Industry Reports
- Market Research Reports on Capacitor Technologies
- Global Semiconductor Alliance Publications
C. Manufacturer Guidelines
- Manufacturer specifications and guidelines for ceramic capacitor production.
This comprehensive overview of the mainstream ceramic capacitor production process highlights the intricate steps involved and the importance of quality control, innovation, and sustainability in meeting the demands of the ever-evolving electronics industry.
What is the Mainstream Ceramic Capacitor Production Process?
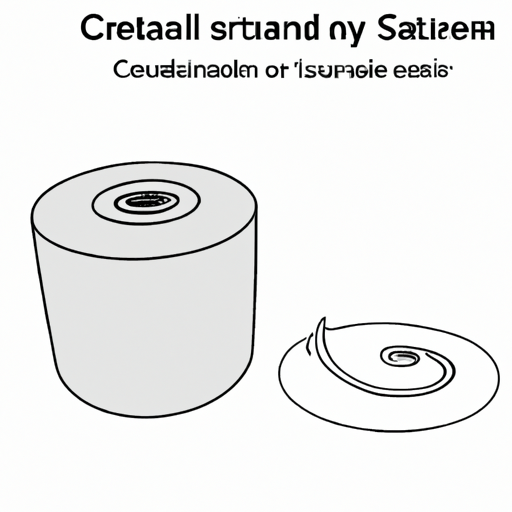
I. Introduction
A. Definition of Ceramic Capacitors
Ceramic capacitors are passive electronic components that store electrical energy in an electric field. They are made from ceramic materials, which are non-metallic and inorganic, and are widely used in various electronic circuits due to their reliability and stability. These capacitors are characterized by their ability to maintain capacitance over a wide range of temperatures and voltages.
B. Importance of Ceramic Capacitors in Electronics
Ceramic capacitors play a crucial role in modern electronics. They are used in applications ranging from filtering and decoupling to timing and energy storage. Their small size, low cost, and high reliability make them ideal for use in consumer electronics, automotive systems, telecommunications, and industrial equipment. As technology advances, the demand for efficient and compact capacitors continues to grow, further emphasizing the importance of ceramic capacitors in the electronics industry.
C. Overview of the Production Process
The production of ceramic capacitors involves several key steps, including material preparation, forming, drying, sintering, electrode application, and final finishing. Each stage is critical to ensuring the quality and performance of the final product. This blog post will delve into the mainstream production process of ceramic capacitors, exploring the materials used, the techniques employed, and the challenges faced by manufacturers.
II. Types of Ceramic Capacitors
A. Class 1 Capacitors
1. Characteristics
Class 1 ceramic capacitors are known for their stability and low loss characteristics. They typically have a dielectric constant of less than 100 and exhibit minimal capacitance change with temperature and voltage variations. This makes them suitable for precision applications.
2. Applications
These capacitors are commonly used in timing circuits, oscillators, and RF applications where stability is paramount.
B. Class 2 Capacitors
1. Characteristics
Class 2 ceramic capacitors have a higher dielectric constant, which allows for greater capacitance in a smaller package. However, they are less stable than Class 1 capacitors, with capacitance values that can vary significantly with temperature and voltage.
2. Applications
Class 2 capacitors are widely used in applications such as decoupling, filtering, and energy storage in power supply circuits.
C. Comparison of Class 1 and Class 2 Capacitors
While Class 1 capacitors are preferred for applications requiring high stability and low loss, Class 2 capacitors are favored for their higher capacitance values and smaller sizes. The choice between the two depends on the specific requirements of the electronic circuit.
III. Raw Materials
A. Types of Ceramic Materials
1. Barium Titanate
Barium titanate (BaTiO3) is the most commonly used dielectric material in ceramic capacitors. It has a high dielectric constant and excellent temperature stability, making it ideal for Class 2 capacitors.
2. Other Materials
Other ceramic materials, such as strontium titanate and lead zirconate titanate, are also used in specific applications, particularly where unique electrical properties are required.
B. Conductive Materials
1. Silver
Silver is the most widely used conductive material for the electrodes of ceramic capacitors due to its excellent conductivity and reliability.
2. Other Metal Oxides
In some cases, other metal oxides, such as nickel or palladium, may be used as alternatives to silver, particularly in cost-sensitive applications.
C. Additives and Their Functions
Additives are often included in the ceramic mixture to enhance specific properties, such as improving sintering behavior, increasing dielectric strength, or modifying the thermal expansion coefficient.
IV. The Production Process
A. Material Preparation
1. Sourcing and Quality Control
The production process begins with sourcing high-quality raw materials. Manufacturers must ensure that the materials meet strict quality standards to achieve the desired electrical properties in the final product.
2. Mixing and Milling
Once the materials are sourced, they are mixed and milled to create a homogeneous powder. This step is crucial, as uneven mixing can lead to inconsistencies in the final product.
B. Forming
1. Methods of Forming
There are several methods for forming ceramic capacitors, including:
Tape Casting: A thin layer of the ceramic mixture is spread onto a substrate and then cut into desired shapes.
Pressing: The ceramic powder is compacted into molds under high pressure to form the capacitor body.
Injection Molding: The ceramic mixture is injected into molds to create complex shapes.
2. Importance of Forming Techniques
The choice of forming technique can significantly impact the density and uniformity of the capacitor, which in turn affects its electrical performance.
C. Drying
1. Purpose of Drying
After forming, the capacitors must be dried to remove any moisture that could affect the sintering process. Proper drying is essential to prevent defects such as cracking or warping.
2. Techniques Used
Common drying techniques include air drying and forced drying in ovens, with careful control of temperature and humidity to ensure uniform drying.
D. Sintering
1. Definition and Importance
Sintering is the process of heating the dried ceramic body to a temperature below its melting point, causing the particles to bond together. This step is critical for achieving the desired mechanical strength and electrical properties.
2. Sintering Process
Temperature Control: The sintering temperature must be carefully controlled to ensure optimal bonding without causing excessive shrinkage or deformation.
Atmosphere Control: The atmosphere in the sintering furnace can also affect the properties of the ceramic. Inert or reducing atmospheres are often used to prevent oxidation of the materials.
E. Electrode Application
1. Methods of Electrode Application
Electrodes are applied to the ceramic body using various methods, including:
Screen Printing: A paste containing conductive materials is printed onto the ceramic surface.
Vapor Deposition: A thin layer of conductive material is deposited onto the ceramic using vapor deposition techniques.
2. Importance of Electrode Quality
The quality of the electrodes is crucial for the overall performance of the capacitor. Poorly applied electrodes can lead to increased resistance and reduced capacitance.
F. Final Finishing
1. Trimming and Testing
After electrode application, the capacitors are trimmed to the desired size and undergo rigorous testing to ensure they meet electrical specifications.
2. Coating and Packaging
Finally, the capacitors are coated for protection and packaged for shipment. Proper packaging is essential to prevent damage during transportation and storage.
V. Quality Control
A. Testing Methods
1. Electrical Testing
Electrical testing is conducted to measure capacitance, dissipation factor, and insulation resistance. These tests ensure that the capacitors meet industry standards.
2. Mechanical Testing
Mechanical testing assesses the physical integrity of the capacitors, including their resistance to mechanical stress and thermal cycling.
B. Standards and Certifications
1. Industry Standards
Manufacturers must adhere to various industry standards, such as those set by the International Electrotechnical Commission (IEC) and the American National Standards Institute (ANSI), to ensure product quality and safety.
2. Environmental Considerations
Environmental regulations also play a role in the production process, with manufacturers required to minimize waste and emissions.
VI. Challenges in Production
A. Material Sourcing Issues
Sourcing high-quality raw materials can be challenging, particularly in a global market where supply chain disruptions can occur.
B. Technological Advancements
As technology evolves, manufacturers must continuously adapt their production processes to incorporate new materials and techniques, which can be both costly and time-consuming.
C. Environmental Impact and Sustainability
The production of ceramic capacitors can have environmental impacts, including waste generation and energy consumption. Manufacturers are increasingly focusing on sustainable practices to mitigate these effects.
VII. Future Trends in Ceramic Capacitor Production
A. Innovations in Materials
Research is ongoing into new ceramic materials that offer improved performance characteristics, such as higher capacitance and better thermal stability.
B. Advances in Production Techniques
Automation and advanced manufacturing techniques, such as 3D printing, are being explored to enhance production efficiency and reduce costs.
C. Market Demand and Growth Projections
The demand for ceramic capacitors is expected to grow, driven by advancements in technology and the increasing use of electronic devices in various industries.
VIII. Conclusion
A. Summary of the Production Process
The production of ceramic capacitors involves a complex series of steps, from material preparation to final finishing. Each stage is critical to ensuring the quality and performance of the final product.
B. Importance of Continuous Improvement
As the electronics industry continues to evolve, manufacturers must prioritize continuous improvement in their production processes to meet changing demands and maintain competitiveness.
C. The Role of Ceramic Capacitors in Future Technologies
Ceramic capacitors will continue to play a vital role in the development of future technologies, supporting innovations in consumer electronics, renewable energy, and beyond.
IX. References
A. Academic Journals
- Journal of Materials Science
- IEEE Transactions on Electronics Packaging Manufacturing
B. Industry Reports
- Market Research Reports on Capacitor Technologies
- Global Semiconductor Alliance Publications
C. Manufacturer Guidelines
- Manufacturer specifications and guidelines for ceramic capacitor production.
This comprehensive overview of the mainstream ceramic capacitor production process highlights the intricate steps involved and the importance of quality control, innovation, and sustainability in meeting the demands of the ever-evolving electronics industry.