What Components and Modules Do Aluminum Electrolytic Capacitors Contain?
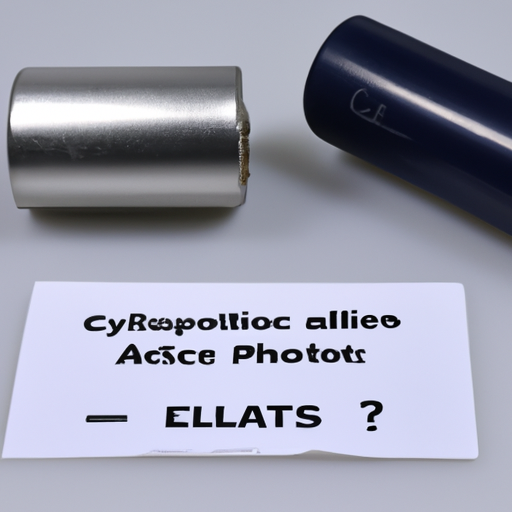
I. Introduction
Aluminum electrolytic capacitors are essential components in modern electronic circuits, playing a crucial role in energy storage, filtering, and voltage regulation. These capacitors are widely used in various applications, from consumer electronics to industrial machinery, due to their high capacitance values and relatively low cost. This article aims to provide a comprehensive overview of the components and modules that make up aluminum electrolytic capacitors, shedding light on their structure, function, and significance in electronic design.
II. Basic Structure of Aluminum Electrolytic Capacitors
A. Anode
The anode of an aluminum electrolytic capacitor is typically made from pure aluminum foil, which is anodized to form a thin layer of aluminum oxide. This oxide layer serves as the dielectric material, crucial for the capacitor's ability to store electrical energy. The surface area of the anode is increased through etching, allowing for greater capacitance. The anode's role in capacitance is fundamental, as it determines the amount of charge the capacitor can hold.
B. Cathode
The cathode is usually composed of a conductive liquid or solid material that interacts with the electrolyte. In many cases, the cathode is formed by a conductive layer on the aluminum foil or by using a conductive paste. The cathode's primary function is to complete the electrical circuit and facilitate the flow of current between the anode and the electrolyte. The interaction between the cathode and the electrolyte is vital for the capacitor's performance, as it influences the overall capacitance and voltage characteristics.
C. Electrolyte
The electrolyte in aluminum electrolytic capacitors can be either liquid or solid, with various formulations available, including aqueous solutions and organic solvents. The choice of electrolyte significantly impacts the capacitor's performance, including its capacitance, leakage current, and temperature stability. The electrolyte serves as the medium through which ions move between the anode and cathode, enabling the capacitor to store and release energy efficiently.
III. Key Components of Aluminum Electrolytic Capacitors
A. Dielectric Layer
The dielectric layer is formed during the anodization process, where the aluminum anode is oxidized to create a thin layer of aluminum oxide. This layer is crucial for the capacitor's operation, as it determines the voltage rating and capacitance. The thickness of the dielectric layer directly affects the capacitor's ability to withstand voltage without breaking down. A thicker dielectric layer can handle higher voltages but may reduce capacitance, while a thinner layer allows for higher capacitance but at the risk of lower voltage tolerance.
B. Leads and Terminals
Aluminum electrolytic capacitors come with leads or terminals that connect the capacitor to the circuit. There are two main types of leads: axial and radial. Axial leads extend from either end of the capacitor, while radial leads emerge from the same end. The choice of lead type depends on the application and the design of the circuit. The material and design of the leads are also important, as they must provide reliable electrical connections while minimizing resistance and heat generation.
C. Housing and Encapsulation
The housing of aluminum electrolytic capacitors is typically made from aluminum or plastic, providing mechanical protection and insulation. The encapsulation process involves sealing the capacitor to protect it from environmental factors such as moisture, dust, and temperature fluctuations. Proper housing and encapsulation are essential for ensuring the longevity and reliability of the capacitor, especially in demanding applications.
IV. Internal Modules and Their Functions
A. Electrolytic Cell
The electrolytic cell is the core component of aluminum electrolytic capacitors, where the actual energy storage occurs. It consists of the anode, cathode, and electrolyte, working together to store electrical energy in the form of an electric field. The efficiency of the electrolytic cell is critical for the overall performance of the capacitor, influencing factors such as capacitance, leakage current, and response time.
B. Venting Mechanism
Aluminum electrolytic capacitors are designed with a venting mechanism to release gas buildup that can occur during operation, especially in the event of failure. This safety feature prevents catastrophic failure by allowing gases to escape safely, reducing the risk of explosion or leakage. The venting mechanism is an essential aspect of capacitor design, ensuring safe operation in various conditions.
C. Insulation and Separation
Insulation plays a vital role in preventing short circuits between the anode and cathode. The dielectric layer acts as an insulator, while additional insulation materials may be used to enhance safety and performance. Proper separation of the anode and cathode is crucial for maintaining the capacitor's functionality and preventing premature failure.
V. Manufacturing Process
A. Overview of the Production Steps
The manufacturing process of aluminum electrolytic capacitors involves several key steps, including the preparation of aluminum foil, anodization, electrolyte filling, and assembly. The aluminum foil is first cleaned and etched to increase its surface area, followed by anodization to form the dielectric layer. Afterward, the electrolyte is introduced, and the capacitor is assembled with leads and housing.
B. Quality Control Measures
Quality control is critical in the production of aluminum electrolytic capacitors to ensure reliability and performance. Manufacturers implement rigorous testing procedures, including electrical testing, visual inspections, and environmental testing, to identify defects and ensure that capacitors meet industry standards.
C. Innovations in Manufacturing Techniques
Recent advancements in manufacturing techniques have led to improved performance and reliability of aluminum electrolytic capacitors. Innovations such as automated production lines, advanced materials, and enhanced testing methods have contributed to the development of capacitors with higher capacitance values, lower leakage currents, and better thermal stability.
VI. Applications of Aluminum Electrolytic Capacitors
A. Common Uses in Electronic Devices
Aluminum electrolytic capacitors are widely used in various electronic devices, including power supplies, audio equipment, and consumer electronics. Their high capacitance values make them ideal for applications requiring significant energy storage and filtering capabilities.
B. Importance in Power Supply Circuits
In power supply circuits, aluminum electrolytic capacitors play a crucial role in smoothing out voltage fluctuations and providing stable power to electronic components. They help filter out noise and ripple, ensuring that devices operate efficiently and reliably.
C. Role in Filtering and Energy Storage
Aluminum electrolytic capacitors are essential in filtering applications, where they help remove unwanted frequencies from signals. They are also used in energy storage applications, providing temporary power during peak demand or when other power sources are unavailable.
VII. Conclusion
In summary, aluminum electrolytic capacitors are complex components composed of various modules and materials that work together to store and release electrical energy. Understanding the key components, such as the anode, cathode, electrolyte, and dielectric layer, is essential for engineers and designers working with electronic circuits. As technology continues to evolve, advancements in aluminum electrolytic capacitor design and manufacturing will likely lead to even greater performance and reliability, making them indispensable in the ever-growing field of electronics.
VIII. References
For further exploration of aluminum electrolytic capacitors, consider the following resources:
1. "Capacitor Technology: A Comprehensive Guide" - A detailed book covering various capacitor technologies, including aluminum electrolytic capacitors.
2. "IEEE Standards for Capacitors" - Industry standards and guidelines related to capacitor design and performance.
3. "Electrolytic Capacitors: Theory and Applications" - A research paper discussing the principles and applications of electrolytic capacitors in electronic circuits.
By understanding the components and modules of aluminum electrolytic capacitors, engineers can make informed decisions in their designs, ensuring optimal performance and reliability in their electronic applications.
What Components and Modules Do Aluminum Electrolytic Capacitors Contain?
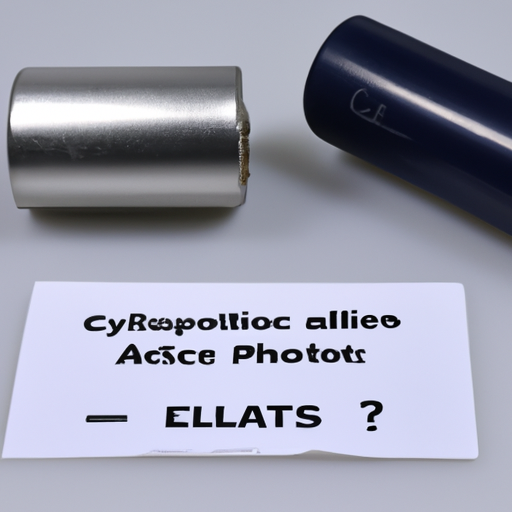
I. Introduction
Aluminum electrolytic capacitors are essential components in modern electronic circuits, playing a crucial role in energy storage, filtering, and voltage regulation. These capacitors are widely used in various applications, from consumer electronics to industrial machinery, due to their high capacitance values and relatively low cost. This article aims to provide a comprehensive overview of the components and modules that make up aluminum electrolytic capacitors, shedding light on their structure, function, and significance in electronic design.
II. Basic Structure of Aluminum Electrolytic Capacitors
A. Anode
The anode of an aluminum electrolytic capacitor is typically made from pure aluminum foil, which is anodized to form a thin layer of aluminum oxide. This oxide layer serves as the dielectric material, crucial for the capacitor's ability to store electrical energy. The surface area of the anode is increased through etching, allowing for greater capacitance. The anode's role in capacitance is fundamental, as it determines the amount of charge the capacitor can hold.
B. Cathode
The cathode is usually composed of a conductive liquid or solid material that interacts with the electrolyte. In many cases, the cathode is formed by a conductive layer on the aluminum foil or by using a conductive paste. The cathode's primary function is to complete the electrical circuit and facilitate the flow of current between the anode and the electrolyte. The interaction between the cathode and the electrolyte is vital for the capacitor's performance, as it influences the overall capacitance and voltage characteristics.
C. Electrolyte
The electrolyte in aluminum electrolytic capacitors can be either liquid or solid, with various formulations available, including aqueous solutions and organic solvents. The choice of electrolyte significantly impacts the capacitor's performance, including its capacitance, leakage current, and temperature stability. The electrolyte serves as the medium through which ions move between the anode and cathode, enabling the capacitor to store and release energy efficiently.
III. Key Components of Aluminum Electrolytic Capacitors
A. Dielectric Layer
The dielectric layer is formed during the anodization process, where the aluminum anode is oxidized to create a thin layer of aluminum oxide. This layer is crucial for the capacitor's operation, as it determines the voltage rating and capacitance. The thickness of the dielectric layer directly affects the capacitor's ability to withstand voltage without breaking down. A thicker dielectric layer can handle higher voltages but may reduce capacitance, while a thinner layer allows for higher capacitance but at the risk of lower voltage tolerance.
B. Leads and Terminals
Aluminum electrolytic capacitors come with leads or terminals that connect the capacitor to the circuit. There are two main types of leads: axial and radial. Axial leads extend from either end of the capacitor, while radial leads emerge from the same end. The choice of lead type depends on the application and the design of the circuit. The material and design of the leads are also important, as they must provide reliable electrical connections while minimizing resistance and heat generation.
C. Housing and Encapsulation
The housing of aluminum electrolytic capacitors is typically made from aluminum or plastic, providing mechanical protection and insulation. The encapsulation process involves sealing the capacitor to protect it from environmental factors such as moisture, dust, and temperature fluctuations. Proper housing and encapsulation are essential for ensuring the longevity and reliability of the capacitor, especially in demanding applications.
IV. Internal Modules and Their Functions
A. Electrolytic Cell
The electrolytic cell is the core component of aluminum electrolytic capacitors, where the actual energy storage occurs. It consists of the anode, cathode, and electrolyte, working together to store electrical energy in the form of an electric field. The efficiency of the electrolytic cell is critical for the overall performance of the capacitor, influencing factors such as capacitance, leakage current, and response time.
B. Venting Mechanism
Aluminum electrolytic capacitors are designed with a venting mechanism to release gas buildup that can occur during operation, especially in the event of failure. This safety feature prevents catastrophic failure by allowing gases to escape safely, reducing the risk of explosion or leakage. The venting mechanism is an essential aspect of capacitor design, ensuring safe operation in various conditions.
C. Insulation and Separation
Insulation plays a vital role in preventing short circuits between the anode and cathode. The dielectric layer acts as an insulator, while additional insulation materials may be used to enhance safety and performance. Proper separation of the anode and cathode is crucial for maintaining the capacitor's functionality and preventing premature failure.
V. Manufacturing Process
A. Overview of the Production Steps
The manufacturing process of aluminum electrolytic capacitors involves several key steps, including the preparation of aluminum foil, anodization, electrolyte filling, and assembly. The aluminum foil is first cleaned and etched to increase its surface area, followed by anodization to form the dielectric layer. Afterward, the electrolyte is introduced, and the capacitor is assembled with leads and housing.
B. Quality Control Measures
Quality control is critical in the production of aluminum electrolytic capacitors to ensure reliability and performance. Manufacturers implement rigorous testing procedures, including electrical testing, visual inspections, and environmental testing, to identify defects and ensure that capacitors meet industry standards.
C. Innovations in Manufacturing Techniques
Recent advancements in manufacturing techniques have led to improved performance and reliability of aluminum electrolytic capacitors. Innovations such as automated production lines, advanced materials, and enhanced testing methods have contributed to the development of capacitors with higher capacitance values, lower leakage currents, and better thermal stability.
VI. Applications of Aluminum Electrolytic Capacitors
A. Common Uses in Electronic Devices
Aluminum electrolytic capacitors are widely used in various electronic devices, including power supplies, audio equipment, and consumer electronics. Their high capacitance values make them ideal for applications requiring significant energy storage and filtering capabilities.
B. Importance in Power Supply Circuits
In power supply circuits, aluminum electrolytic capacitors play a crucial role in smoothing out voltage fluctuations and providing stable power to electronic components. They help filter out noise and ripple, ensuring that devices operate efficiently and reliably.
C. Role in Filtering and Energy Storage
Aluminum electrolytic capacitors are essential in filtering applications, where they help remove unwanted frequencies from signals. They are also used in energy storage applications, providing temporary power during peak demand or when other power sources are unavailable.
VII. Conclusion
In summary, aluminum electrolytic capacitors are complex components composed of various modules and materials that work together to store and release electrical energy. Understanding the key components, such as the anode, cathode, electrolyte, and dielectric layer, is essential for engineers and designers working with electronic circuits. As technology continues to evolve, advancements in aluminum electrolytic capacitor design and manufacturing will likely lead to even greater performance and reliability, making them indispensable in the ever-growing field of electronics.
VIII. References
For further exploration of aluminum electrolytic capacitors, consider the following resources:
1. "Capacitor Technology: A Comprehensive Guide" - A detailed book covering various capacitor technologies, including aluminum electrolytic capacitors.
2. "IEEE Standards for Capacitors" - Industry standards and guidelines related to capacitor design and performance.
3. "Electrolytic Capacitors: Theory and Applications" - A research paper discussing the principles and applications of electrolytic capacitors in electronic circuits.
By understanding the components and modules of aluminum electrolytic capacitors, engineers can make informed decisions in their designs, ensuring optimal performance and reliability in their electronic applications.