What are the Manufacturing Processes of the Latest Automotive Capacitors?
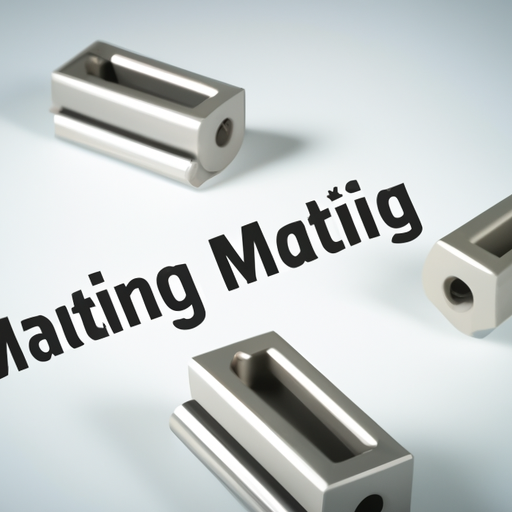
I. Introduction
In the rapidly evolving automotive industry, capacitors play a crucial role in ensuring the efficiency and reliability of modern vehicles. Automotive capacitors are electronic components that store and release electrical energy, serving various functions such as filtering, energy storage, and power management. As vehicles become increasingly sophisticated, the demand for high-performance capacitors has surged, leading to advancements in manufacturing processes. This article aims to explore the types of automotive capacitors, the key manufacturing processes involved, the challenges faced, and future trends shaping the industry.
II. Types of Automotive Capacitors
A. Ceramic Capacitors
Ceramic capacitors are widely used in automotive applications due to their stability and reliability. They are characterized by their small size, high capacitance-to-volume ratio, and ability to operate over a wide temperature range. Common applications include decoupling, filtering, and timing circuits in electronic control units (ECUs).
B. Electrolytic Capacitors
Electrolytic capacitors are known for their high capacitance values, making them ideal for applications requiring significant energy storage, such as power supply circuits and energy recovery systems. They consist of a dielectric layer formed by an oxide film, which is created through an electrochemical process.
C. Film Capacitors
Film capacitors are constructed using thin plastic films as the dielectric material. They offer excellent stability, low self-inductance, and high insulation resistance, making them suitable for high-frequency applications. In automotive systems, they are often used in power electronics and motor drives.
D. Supercapacitors
Supercapacitors, or ultracapacitors, bridge the gap between traditional capacitors and batteries. They provide high energy density and rapid charge/discharge capabilities, making them ideal for applications such as regenerative braking systems and energy storage in hybrid and electric vehicles.
III. Key Manufacturing Processes
A. Material Selection
The manufacturing of automotive capacitors begins with careful material selection. The choice of dielectric and conductive materials is critical to achieving the desired performance characteristics.
1. Dielectric Materials
Dielectric materials, such as ceramic, polymer, or electrolytic solutions, determine the capacitor's capacitance, voltage rating, and temperature stability. For instance, ceramic materials are often chosen for their high dielectric constant and stability, while electrolytic capacitors rely on oxide layers formed on conductive substrates.
2. Conductive Materials
Conductive materials, typically metals like aluminum or tantalum, are used for the electrodes. The choice of conductive material affects the capacitor's efficiency, longevity, and overall performance.
B. Component Fabrication
Once materials are selected, the next step is component fabrication, which involves producing the dielectric layer and electrodes.
1. Dielectric Layer Production
a. Thin Film Deposition
For film capacitors, thin film deposition techniques, such as sputtering or chemical vapor deposition (CVD), are employed to create uniform dielectric layers. These methods allow for precise control over thickness and composition, ensuring optimal performance.
b. Ceramic Processing
In the case of ceramic capacitors, the dielectric material is processed into a powder, which is then shaped and sintered at high temperatures to form a solid ceramic body. This process enhances the dielectric properties and mechanical strength of the capacitor.
2. Electrode Fabrication
a. Metal Deposition Techniques
Electrode fabrication involves depositing conductive materials onto the dielectric layer. Techniques such as physical vapor deposition (PVD) or screen printing are commonly used to create the electrodes, ensuring good electrical contact and adhesion.
b. Etching Processes
Etching processes are employed to define the electrode patterns and remove excess material, allowing for precise control over the capacitor's dimensions and performance characteristics.
C. Assembly Techniques
After individual components are fabricated, they are assembled into the final capacitor structure.
1. Layer Stacking
For multi-layer capacitors, layer stacking is a critical process. Layers of dielectric and electrode materials are stacked and pressed together to form a compact structure. This technique enhances capacitance and reduces equivalent series resistance (ESR).
2. Encapsulation Methods
Encapsulation protects the capacitor from environmental factors and mechanical stress. Various methods, such as resin coating or potting, are used to ensure durability and reliability in automotive applications.
D. Quality Control and Testing
Quality control is paramount in capacitor manufacturing, especially for automotive applications where reliability is crucial.
1. Electrical Testing
Electrical testing involves measuring capacitance, ESR, and leakage current to ensure that the capacitors meet specified performance criteria. Automated testing systems are often employed to enhance efficiency and accuracy.
2. Environmental Testing
Environmental testing assesses the capacitor's performance under extreme conditions, such as temperature fluctuations, humidity, and vibration. This testing ensures that the capacitors can withstand the harsh environments typical in automotive applications.
3. Reliability Testing
Reliability testing, including life cycle testing and accelerated aging tests, evaluates the long-term performance of capacitors. This process helps identify potential failure modes and ensures that the capacitors will perform reliably throughout their intended lifespan.
IV. Advanced Manufacturing Technologies
The automotive capacitor manufacturing landscape is evolving with the integration of advanced technologies.
A. Automation in Capacitor Production
Automation plays a significant role in enhancing production efficiency and consistency. Automated assembly lines and robotic systems streamline the manufacturing process, reducing human error and increasing output.
B. Use of Nanotechnology
Nanotechnology is being explored to improve capacitor performance. By manipulating materials at the nanoscale, manufacturers can enhance dielectric properties, increase energy density, and reduce size.
C. 3D Printing in Capacitor Design
3D printing technology is emerging as a viable method for producing complex capacitor geometries. This approach allows for rapid prototyping and customization, enabling manufacturers to innovate and respond to market demands more effectively.
D. Integration of IoT for Real-Time Monitoring
The integration of the Internet of Things (IoT) in capacitor manufacturing enables real-time monitoring of production processes. This technology allows manufacturers to track performance metrics, identify issues promptly, and optimize production efficiency.
V. Challenges in Manufacturing Automotive Capacitors
Despite advancements, several challenges persist in the manufacturing of automotive capacitors.
A. Material Sourcing and Sustainability
The sourcing of raw materials, particularly rare metals used in capacitors, poses sustainability challenges. Manufacturers are increasingly seeking alternative materials and recycling methods to reduce environmental impact.
B. Meeting Stringent Automotive Standards
Automotive capacitors must meet rigorous industry standards for safety, performance, and reliability. Navigating these standards can be complex and requires continuous investment in research and development.
C. Balancing Performance and Cost
Manufacturers face the challenge of balancing high performance with cost-effectiveness. As demand for advanced capacitors grows, finding ways to reduce production costs while maintaining quality is essential.
D. Innovations in Recycling and Waste Management
As the automotive industry shifts towards sustainability, innovations in recycling and waste management are becoming increasingly important. Developing efficient recycling processes for capacitors can help reduce environmental impact and promote a circular economy.
VI. Future Trends in Automotive Capacitor Manufacturing
The future of automotive capacitor manufacturing is poised for significant advancements.
A. Development of New Materials
Research into new dielectric and conductive materials is ongoing, with the potential to enhance performance and reduce costs. Innovations in materials science will likely lead to the development of capacitors with improved energy density and efficiency.
B. Miniaturization and Increased Efficiency
As vehicles become more compact and technology-driven, the demand for smaller, more efficient capacitors will grow. Manufacturers will focus on miniaturization without compromising performance.
C. Enhanced Performance for Electric and Hybrid Vehicles
The rise of electric and hybrid vehicles is driving the need for capacitors that can handle higher voltages and energy densities. Future capacitors will be designed to meet the specific requirements of these advanced powertrains.
D. Impact of Autonomous Vehicles on Capacitor Design
The advent of autonomous vehicles will influence capacitor design, as these vehicles require advanced electronic systems for navigation, communication, and safety. Capacitors will need to support the increased power demands and reliability required for these systems.
VII. Conclusion
In conclusion, automotive capacitors are essential components that contribute to the performance and reliability of modern vehicles. Understanding the manufacturing processes, from material selection to assembly and testing, is crucial for ensuring high-quality capacitors that meet the demands of the automotive industry. As technology continues to evolve, manufacturers will face challenges and opportunities that will shape the future of automotive capacitors. The ongoing development of new materials, advanced manufacturing techniques, and a focus on sustainability will drive innovation in this critical sector, ensuring that automotive capacitors remain at the forefront of automotive technology.
VIII. References
- Academic journals on capacitor technology and automotive electronics.
- Industry reports on trends in automotive manufacturing and electronic components.
- Manufacturer specifications and guidelines for automotive capacitors.
What are the Manufacturing Processes of the Latest Automotive Capacitors?
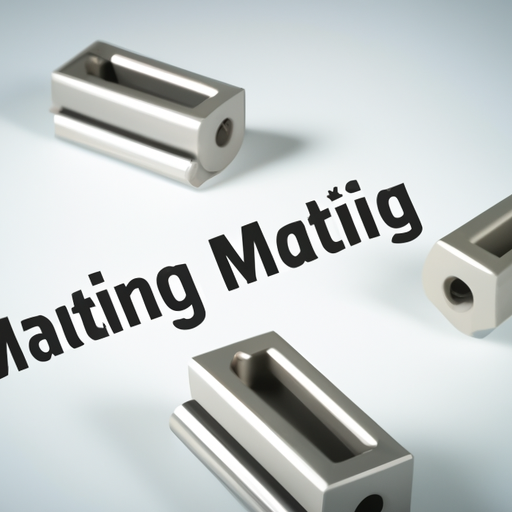
I. Introduction
In the rapidly evolving automotive industry, capacitors play a crucial role in ensuring the efficiency and reliability of modern vehicles. Automotive capacitors are electronic components that store and release electrical energy, serving various functions such as filtering, energy storage, and power management. As vehicles become increasingly sophisticated, the demand for high-performance capacitors has surged, leading to advancements in manufacturing processes. This article aims to explore the types of automotive capacitors, the key manufacturing processes involved, the challenges faced, and future trends shaping the industry.
II. Types of Automotive Capacitors
A. Ceramic Capacitors
Ceramic capacitors are widely used in automotive applications due to their stability and reliability. They are characterized by their small size, high capacitance-to-volume ratio, and ability to operate over a wide temperature range. Common applications include decoupling, filtering, and timing circuits in electronic control units (ECUs).
B. Electrolytic Capacitors
Electrolytic capacitors are known for their high capacitance values, making them ideal for applications requiring significant energy storage, such as power supply circuits and energy recovery systems. They consist of a dielectric layer formed by an oxide film, which is created through an electrochemical process.
C. Film Capacitors
Film capacitors are constructed using thin plastic films as the dielectric material. They offer excellent stability, low self-inductance, and high insulation resistance, making them suitable for high-frequency applications. In automotive systems, they are often used in power electronics and motor drives.
D. Supercapacitors
Supercapacitors, or ultracapacitors, bridge the gap between traditional capacitors and batteries. They provide high energy density and rapid charge/discharge capabilities, making them ideal for applications such as regenerative braking systems and energy storage in hybrid and electric vehicles.
III. Key Manufacturing Processes
A. Material Selection
The manufacturing of automotive capacitors begins with careful material selection. The choice of dielectric and conductive materials is critical to achieving the desired performance characteristics.
1. Dielectric Materials
Dielectric materials, such as ceramic, polymer, or electrolytic solutions, determine the capacitor's capacitance, voltage rating, and temperature stability. For instance, ceramic materials are often chosen for their high dielectric constant and stability, while electrolytic capacitors rely on oxide layers formed on conductive substrates.
2. Conductive Materials
Conductive materials, typically metals like aluminum or tantalum, are used for the electrodes. The choice of conductive material affects the capacitor's efficiency, longevity, and overall performance.
B. Component Fabrication
Once materials are selected, the next step is component fabrication, which involves producing the dielectric layer and electrodes.
1. Dielectric Layer Production
a. Thin Film Deposition
For film capacitors, thin film deposition techniques, such as sputtering or chemical vapor deposition (CVD), are employed to create uniform dielectric layers. These methods allow for precise control over thickness and composition, ensuring optimal performance.
b. Ceramic Processing
In the case of ceramic capacitors, the dielectric material is processed into a powder, which is then shaped and sintered at high temperatures to form a solid ceramic body. This process enhances the dielectric properties and mechanical strength of the capacitor.
2. Electrode Fabrication
a. Metal Deposition Techniques
Electrode fabrication involves depositing conductive materials onto the dielectric layer. Techniques such as physical vapor deposition (PVD) or screen printing are commonly used to create the electrodes, ensuring good electrical contact and adhesion.
b. Etching Processes
Etching processes are employed to define the electrode patterns and remove excess material, allowing for precise control over the capacitor's dimensions and performance characteristics.
C. Assembly Techniques
After individual components are fabricated, they are assembled into the final capacitor structure.
1. Layer Stacking
For multi-layer capacitors, layer stacking is a critical process. Layers of dielectric and electrode materials are stacked and pressed together to form a compact structure. This technique enhances capacitance and reduces equivalent series resistance (ESR).
2. Encapsulation Methods
Encapsulation protects the capacitor from environmental factors and mechanical stress. Various methods, such as resin coating or potting, are used to ensure durability and reliability in automotive applications.
D. Quality Control and Testing
Quality control is paramount in capacitor manufacturing, especially for automotive applications where reliability is crucial.
1. Electrical Testing
Electrical testing involves measuring capacitance, ESR, and leakage current to ensure that the capacitors meet specified performance criteria. Automated testing systems are often employed to enhance efficiency and accuracy.
2. Environmental Testing
Environmental testing assesses the capacitor's performance under extreme conditions, such as temperature fluctuations, humidity, and vibration. This testing ensures that the capacitors can withstand the harsh environments typical in automotive applications.
3. Reliability Testing
Reliability testing, including life cycle testing and accelerated aging tests, evaluates the long-term performance of capacitors. This process helps identify potential failure modes and ensures that the capacitors will perform reliably throughout their intended lifespan.
IV. Advanced Manufacturing Technologies
The automotive capacitor manufacturing landscape is evolving with the integration of advanced technologies.
A. Automation in Capacitor Production
Automation plays a significant role in enhancing production efficiency and consistency. Automated assembly lines and robotic systems streamline the manufacturing process, reducing human error and increasing output.
B. Use of Nanotechnology
Nanotechnology is being explored to improve capacitor performance. By manipulating materials at the nanoscale, manufacturers can enhance dielectric properties, increase energy density, and reduce size.
C. 3D Printing in Capacitor Design
3D printing technology is emerging as a viable method for producing complex capacitor geometries. This approach allows for rapid prototyping and customization, enabling manufacturers to innovate and respond to market demands more effectively.
D. Integration of IoT for Real-Time Monitoring
The integration of the Internet of Things (IoT) in capacitor manufacturing enables real-time monitoring of production processes. This technology allows manufacturers to track performance metrics, identify issues promptly, and optimize production efficiency.
V. Challenges in Manufacturing Automotive Capacitors
Despite advancements, several challenges persist in the manufacturing of automotive capacitors.
A. Material Sourcing and Sustainability
The sourcing of raw materials, particularly rare metals used in capacitors, poses sustainability challenges. Manufacturers are increasingly seeking alternative materials and recycling methods to reduce environmental impact.
B. Meeting Stringent Automotive Standards
Automotive capacitors must meet rigorous industry standards for safety, performance, and reliability. Navigating these standards can be complex and requires continuous investment in research and development.
C. Balancing Performance and Cost
Manufacturers face the challenge of balancing high performance with cost-effectiveness. As demand for advanced capacitors grows, finding ways to reduce production costs while maintaining quality is essential.
D. Innovations in Recycling and Waste Management
As the automotive industry shifts towards sustainability, innovations in recycling and waste management are becoming increasingly important. Developing efficient recycling processes for capacitors can help reduce environmental impact and promote a circular economy.
VI. Future Trends in Automotive Capacitor Manufacturing
The future of automotive capacitor manufacturing is poised for significant advancements.
A. Development of New Materials
Research into new dielectric and conductive materials is ongoing, with the potential to enhance performance and reduce costs. Innovations in materials science will likely lead to the development of capacitors with improved energy density and efficiency.
B. Miniaturization and Increased Efficiency
As vehicles become more compact and technology-driven, the demand for smaller, more efficient capacitors will grow. Manufacturers will focus on miniaturization without compromising performance.
C. Enhanced Performance for Electric and Hybrid Vehicles
The rise of electric and hybrid vehicles is driving the need for capacitors that can handle higher voltages and energy densities. Future capacitors will be designed to meet the specific requirements of these advanced powertrains.
D. Impact of Autonomous Vehicles on Capacitor Design
The advent of autonomous vehicles will influence capacitor design, as these vehicles require advanced electronic systems for navigation, communication, and safety. Capacitors will need to support the increased power demands and reliability required for these systems.
VII. Conclusion
In conclusion, automotive capacitors are essential components that contribute to the performance and reliability of modern vehicles. Understanding the manufacturing processes, from material selection to assembly and testing, is crucial for ensuring high-quality capacitors that meet the demands of the automotive industry. As technology continues to evolve, manufacturers will face challenges and opportunities that will shape the future of automotive capacitors. The ongoing development of new materials, advanced manufacturing techniques, and a focus on sustainability will drive innovation in this critical sector, ensuring that automotive capacitors remain at the forefront of automotive technology.
VIII. References
- Academic journals on capacitor technology and automotive electronics.
- Industry reports on trends in automotive manufacturing and electronic components.
- Manufacturer specifications and guidelines for automotive capacitors.